Blog
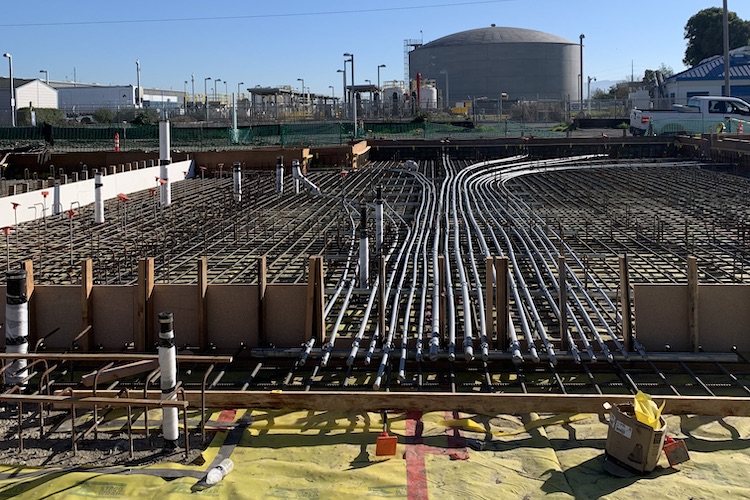
Can Collaborative Delivery Help Owners Manage Market Volatility and Provide Cost Control?
Simply put, yes. The last two years plus have been remarkable in terms of dynamic and compounding events affecting the global supply chain, thus resulting in market uncertainty.
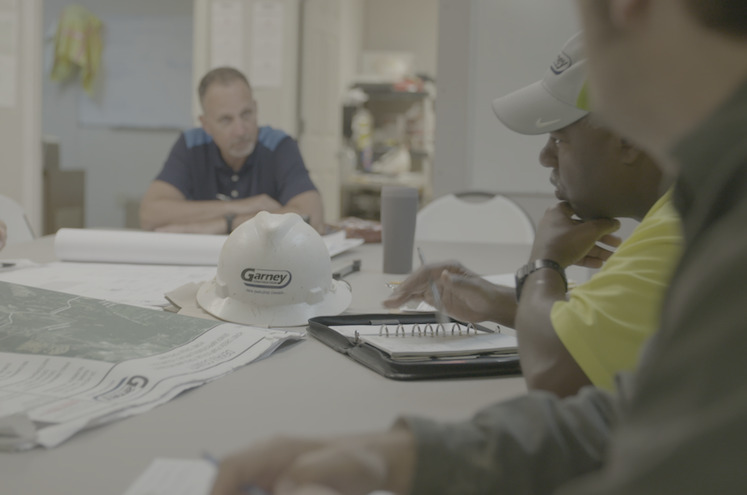
Helpful Preplanning Tips for a Collaborative Delivery Project
Collaborative delivery projects almost always begin with the project team having the mindset that the project will be completed safely, within budget, and on time.
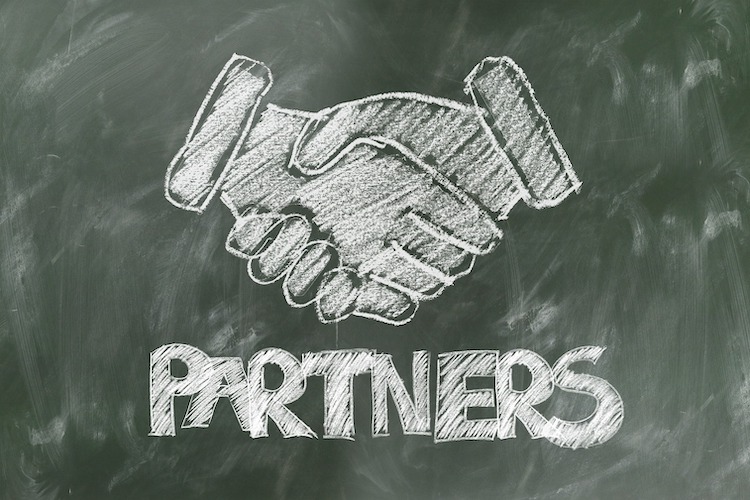
Unlocking the Potential of Progressive Design-Build Teaming Arrangements with the Integrated Joint Venture Model
Collaborative delivery offers owners the opportunity to access the talents and resources of design and construction professionals in a manner unlike traditional delivery methods.
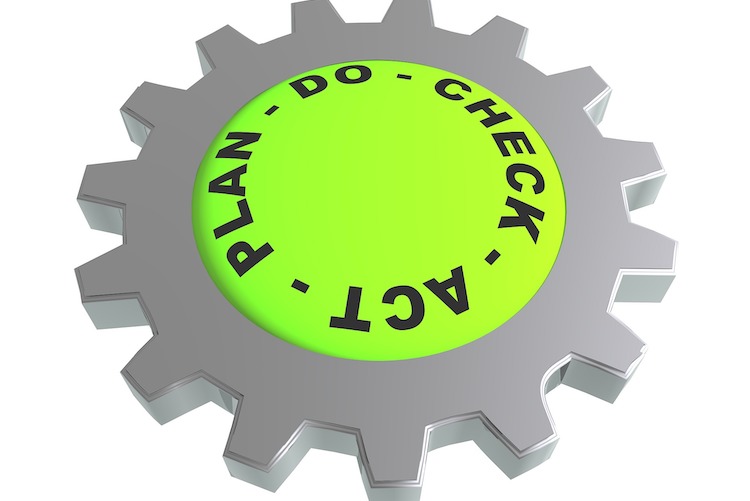
Catch a Break: How to Reduce Construction Fatigue at Your Facility
My wife and I tell our guests to make themselves at home, but this can quickly go awry. Several years ago, with only two months until our first child was due, we decided to buy a fixer-upper and start a complete “gut and rebuild.”
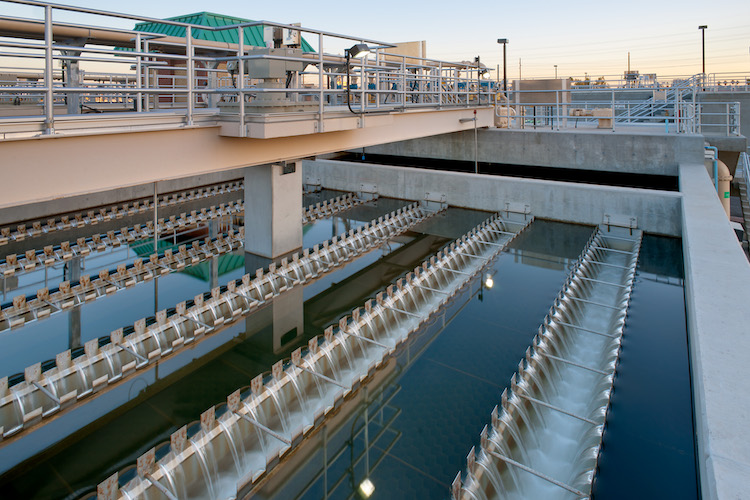
Early Works Strategies in a Volatile Market
When the supply chain faces pressure and creates a volatile market for utility-scale construction projects, challenges arise for project teams seeking solutions to long-term wastewater treatment facility expansions.
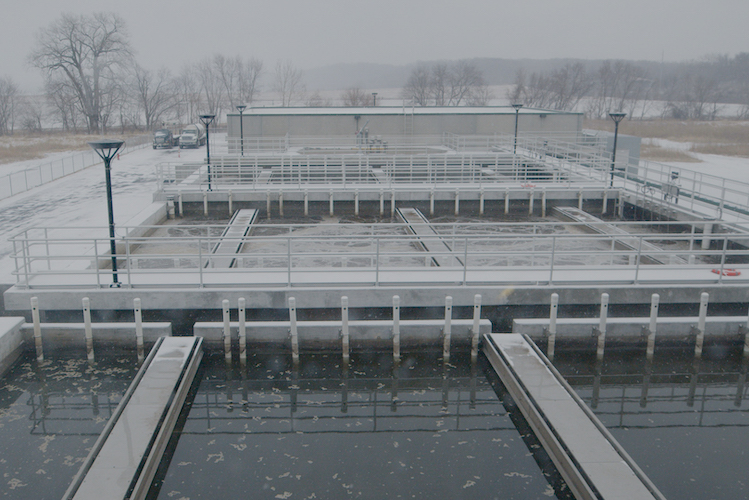
Benefits of Construction Management at-Risk from an Owner’s Perspective
HDR and Garney recently conducted an interview with the UG project team to gain insight into some of the tangible benefits it has realized through its recent CMAR procurements.
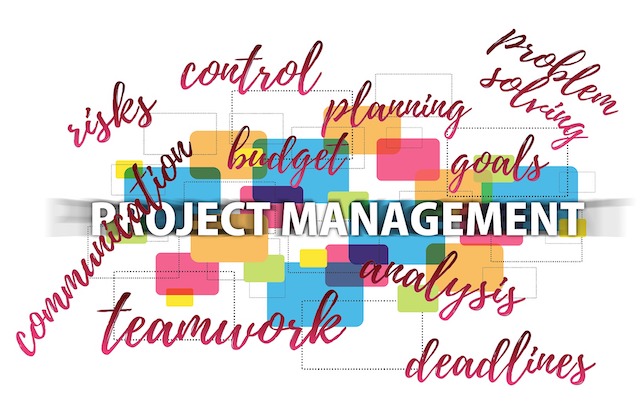
Fast-Track the Implementation of Your Next Project by Leveraging CPD and enlisting an Owner Advisor
How do you keep complex projects on track and successfully moving forward? Collaborative project delivery (CPD) combined with the use of an owner advisor (OA) or program manager.
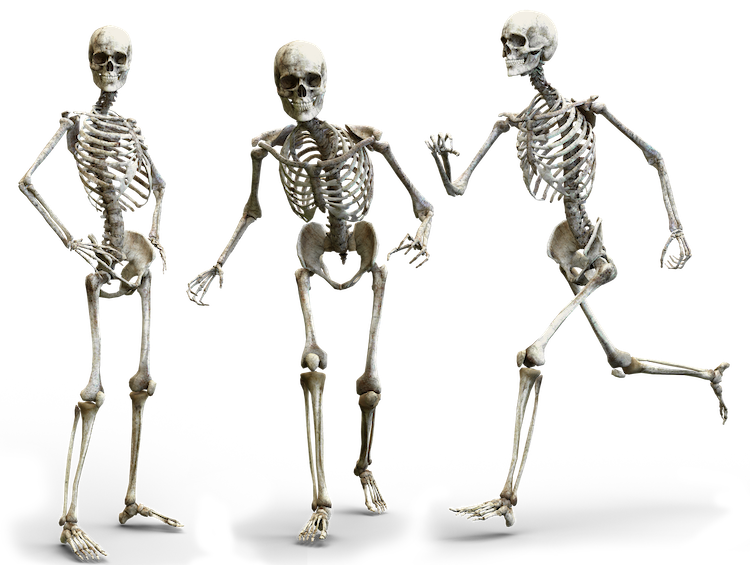
THE “STAND, WALK, RUN” APPROACH TO CLOSING OUT WASTEWATER CONSTRUCTION PROJECTS
As construction projects at wastewater treatment plants near completion, everyone involved usually has a bit of fatigue.
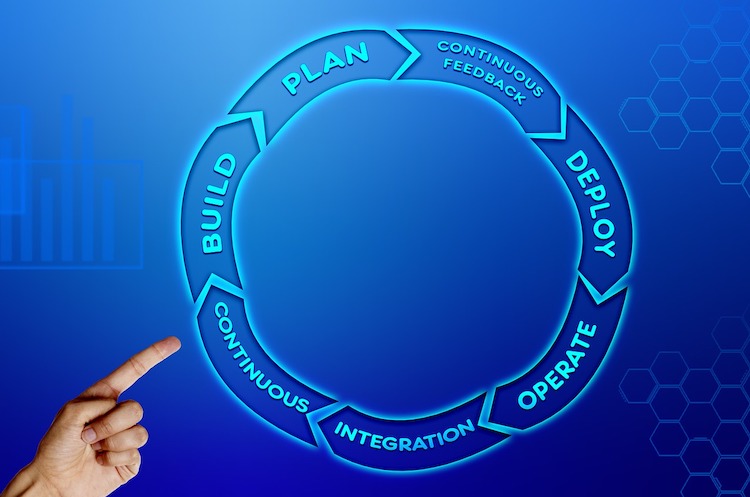
Transparent Collaboration Maximizes Value on Big Projects
Collaboration, innovation, and inclusion are key to the success of big design-build projects. Implementing such measures in the early phases of a project helps ensure overall project success and should be a guiding principle on all large design-build projects.
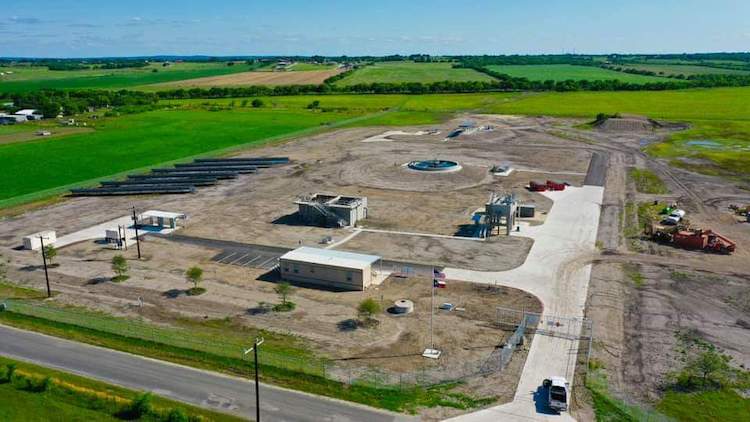
Silver Lining: Lessons Learned from an Envision-Rated Treatment Plant
Sustainability has become a word mentioned across our lives and the industry but isn’t as clearly defined as other terms like efficiency, safety factor, or effluent quality.