In real estate, the mantra “location, location, location” means choosing the wrong site for a development could cost you dearly later. In construction, the same can be said for document control—one wrong decision could have costly consequences. From a general contractor’s perspective, I’ve seen many document control mistakes, specifically in the design-bid-build delivery method. For example, if the field crews don’t receive a change in dimensions from the request for information (RFI), they’re faced with potential rework, cost impacts, and schedule delays.
As the industry advances toward more collaborative delivery methods, document control for the 30%, 60%, and 100% contract documents adds another layer of difficulty. Challenges arise in managing everything from cost estimates to the release of long-lead materials at the 30% or 60% phase while ensuring everyone has the latest drawings. While this form of document control might be common for larger design firms, subcontractors, vendors, suppliers, and smaller firms often aren’t exposed to the collaborative delivery method. Some design firms might not recognize the importance of achieving 100% design completion to release long-lead items, even when the design is only 30% complete. Subcontractors and vendors might not have the staff to consistently update pricing or evaluate changes.
From a pricing perspective, outdated drawings on larger projects will not cause drastic changes in cost simply because the subcontractors’ scopes are smaller. However, there is more risk of fluctuating costs associated with a guaranteed maximum price (GMP) for a small project that relies on small subcontractors and vendors. So how do we manage this risk? By building and maintaining subcontractor relationships through open and consistent communication. Increasing the contingencies and gaining a full understanding of the Basis of Design Report (BODR) are some other good strategies.
Adding a contingency to a GMP to cover costs can work, but it only addresses the cost elements. It’s also important to consider schedule and quality. Moving from design-bid-build delivery to progressive design-build means a high-quality project is delivered to the owner, since quality usually correlates to minimal rework.
Document control is connected to all these scenarios. A full understanding of the BODR, including what’s being procured, ensures the correct drawings and specifications go from the designer to estimators, subcontractors, and vendors. The question is: How many people actually read and understand a BODR? Consider the last time you’ve read the front-end documents or specifications of a report. Reading and, most importantly, understanding the BODR can provide insight into the project’s design, identify unknowns, and help you understand the decisions the owner still has to make.
Since contractors are responsible for managing a GMP and rely on the designer for a project’s design, they need a clear understanding of the decisions that have to be made during the drawing development phase. This clarity helps contractors price a conceptual estimate that leads to the final GMP. Understanding the BODR also ensures that a designer has developed sufficient drawings that include the proper scope and project-specific specifications. Subcontractors and vendors also benefit from a better understanding of the BODR because it allows them to purchase the right equipment and material.
Effective document control is important in all methods of project delivery and for projects of all sizes. I see a higher risk associated with smaller companies. I also see issues arising that could be mitigated if the general contractor has a full understanding of the BODR. Both takeaways minimize costs and risks, improve client relationships, and contribute to project success.
Document Control: An Essential Piece of a successful Collaborative Delivery project
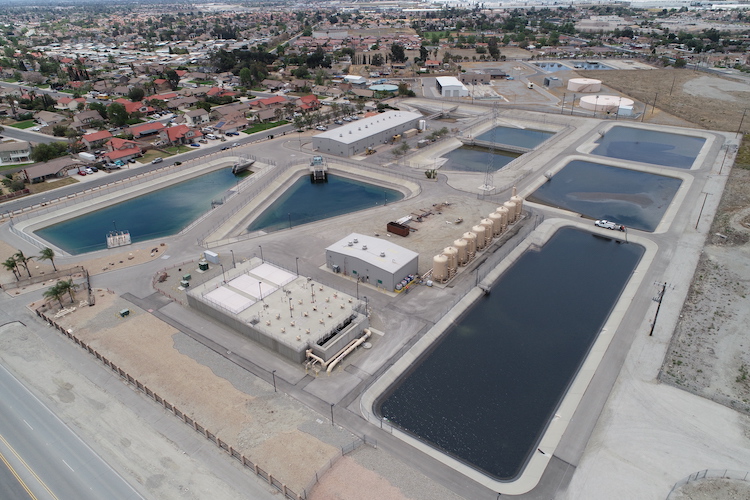