The construction industry faces a significant challenge: achieving ambitious sustainability goals while delivering projects on time and within budget. Traditional, siloed project delivery methods often struggle to address these goals effectively.
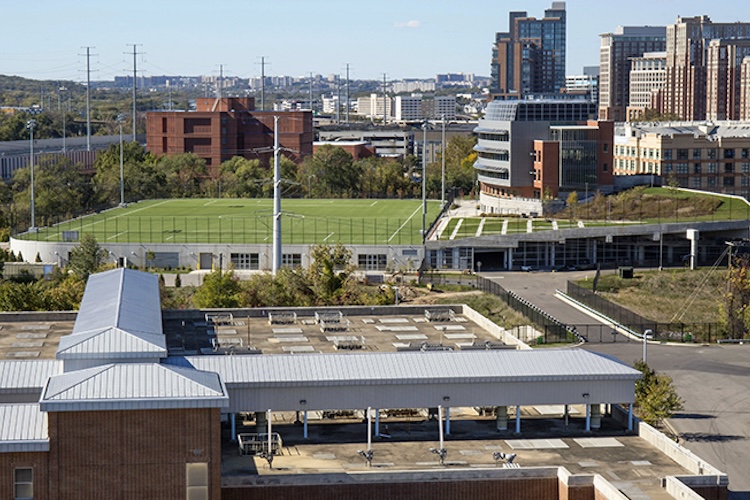
by Ben Miller, Business Development Manager | Ferguson Waterworks
The construction industry faces a significant challenge: achieving ambitious sustainability goals while delivering projects on time and within budget. Traditional, siloed project delivery methods often struggle to address these goals effectively.
by Erik L. Anderson, PE, Assoc. DBIA, Director of Collaborative Delivery | Wharton-Smith
Has anyone been left scratching your head wondering, “Why is my project over budget? What could I have done better to align project budget and cost?”
by Steven Lynk, PE, BCEE, DBIA, Senior Vice President | CDM Smith and Tom Visosky, PE, Senior Vice President–Project Development - Construction | CDM Smith
Collaboration, innovation, and inclusion are key to the success of big design-build projects. Implementing such measures in the early phases of a project helps ensure overall project success and should be a guiding principle on all large design-build projects.
by Shane Lippert, Assoc. DBIA, Vice President – Water Group | Clark Construction
As the number and size of infrastructure projects continue to increase, while the qualified available workforce continues to decrease, contractors who traditionally identify as “self-performing” contractors find themselves having to make decisions on what scopes of work they ultimately need to self-perform for project success. This is especially true on the “mega-sized” projects.
by Michael C. Loulakis, Esq., FDBIA, President | Capital Project Strategies, LLC | WCDA Outside Director
One of my typical roles as an owner advisor is to review proposed construction management at-risk (CMAR) and design-build contracts from a commercial perspective—i.e., what’s the likely marketplace reaction to the contract and is the contract consistent with the philosophy behind collaborative delivery? I am continually amazed by what I see.
by Wesley A. Smith, Director of Business Development – Design-Build | Black & Veatch and Justin Sobol, PMP, DBIA, Director of Project Development – Design-Build Water East Region | Black & Veatch
What happens when your project has a fixed budget and an open-ended project scope? Or what if there is a desire to deal with not only a specific need, but also address a “wish list” of additional improvements?
by Jana Bendinelli, Senior Strategic Writer – Water Marketing Team | Garver and Kyle M. Kruger, PE, DBIA, Water Implementation Leader | Garver
Across the board, supply chain issues and rising costs are impacting engineering and construction projects. The costs of construction materials have elevated over the past year due to growing demand and major disruptions to production fueled by the pandemic. These disruptions are responsible for construction material shortages much like the auto industry is facing with microchip shortages.
by Grant Johnson, BIM Construction Professional | MWH Constructors
The term BIM (Building Information Modeling) has the power to make a seasoned construction veteran cringe. I get it. BIM may sound scary to those who have not used its full advantages. A foreman once told me, “I’m not going to let a Nintendo tell me how to do my job!” Fair enough, but when applied appropriately, BIM can benefit building projects in a variety of ways by aiding design planning, coordination, construction, operations, and facilities management.
by Tracy Streeter, Business Development Manager – Water Group | Burns & McDonnell
The ongoing COVID-19 pandemic has had a significant impact on the continued development of critical infrastructure, creating growing uncertainty concerning financing opportunities and project delivery.
by Michaela Rempkowski, PE, Integrated Design Manager | McCarthy Water
The idea of an integrated design management role for collaborative delivery projects is not a new one. For over 20 years, vertical commercial collaborative delivery projects have assigned an integrated design manager to drive seamless collaboration for overall project success. However, when describing this position in the water industry, the immediate response is, “What is an integrated design manager?”
DC ST § 2–356.01. Project delivery methods authorized.
https://code.dccouncil.gov/us/dc/council/code/sections/2-356.01
(a) This subchapter shall govern procurements for construction projects and related management services in the District.
(b) The following project delivery methods are authorized for procurements within the scope of this subchapter:
(1) Architectural and engineering services;
(2) Construction management;
(3) Construction management at risk;
(4) Design-bid-build;
(5) Design-build;
(6) Design-build-finance-operate-maintain;
(7) Design-build-operate-maintain; and
(8) Operations and maintenance.
P3:
DC ST §§ 2-271.01- 2-275.01
https://code.dccouncil.gov/us/dc/council/code/titles/2/chapters/2A
(11) “Public-private partnership” means the method in the District for delivering a qualified project using a long-term, performance-based agreement between a public entity and a private entity or entities where appropriate risks and benefits can be allocated in a cost-effective manner between the public and private entities in which:
(A) A private entity performs functions normally undertaken by the government, but the public entity remains ultimately accountable for the qualified project and its public function; and
(B) The District may retain ownership or control in the project asset and the private entity may be given additional decision-making rights in determining how the asset is financed, developed, constructed, operated, and maintained over its life cycle.
W.S. § 16-6-701 – 708
https://wyoleg.gov/NXT/gateway.dll?f=templates&fn=default.htm
(a) As used in this act:
v) “Alternate design and construction delivery method” means the delivery method described by any qualifications-based procurement of design and construction services, including all procedures, actions, events, contractual relationships, obligations and forms of agreement for the successful completion of any public work, other than by design, bid and build. Alternate design and construction delivery methods available to a public entity include construction manager agent, construction manager at-risk or design-builder;
(ix) “Design-build” means a type of construction delivery method in which there is a single contract between the public entity and a design-builder who furnishes architectural, engineering and other related design services as required for the public work, as well as labor, materials and other construction services necessary for the public work. A design-builder may be selected by the public entity based on evaluation of responses to a request for qualifications, fixed scope request for proposal or fixed price request for proposal. The following shall apply:
(A) A design-builder may be selected based solely on a response to a request for qualification for public works with an estimated construction cost of five hundred thousand dollars ($500,000.00) or less provided there are not less than two (2) respondents;
(B) Responses to a fixed scope request for proposal or a fixed price request for proposal shall be used as the bases for selection for a public work with an estimated construction cost of more than five hundred thousand dollars ($500,000.00);
(C) Interested parties shall first respond to a request for qualification. Based on responses to the request for qualification a minimum of two (2) and maximum of five (5) respondents may be selected to respond to a fixed scope request for proposal or a fixed price request for proposal;
(D) The respondent chosen by evaluation to provide the best overall value for the public work shall be selected in response to a fixed scope request for proposal or a fixed price request for proposal. The best overall value shall be determined based on criteria set forth by the public entity letting the public work and may include, but is not limited to, qualifications, price, quality of materials and products, past experience and schedule;
W.S. § 16-6-1001 Capital construction projects restrictions; preference requirements; waivers.
https://wyoleg.gov/NXT/gateway.dll?f=templates&fn=default.htm
(i) This paragraph shall apply to any alternate design and construction delivery method as defined in W.S. 16-6-701(a)(v):
(A) All contracts shall require the construction manager at risk or design builder to conduct an open bid process in compliance with Wyoming contractor preference laws before awarding any subcontracts for work covered under the contract;
WS § 13.48(19)
https://docs.legis.wisconsin.gov/statutes/statutes/13/II/48/19
(19) Alternatives to state construction.
(a) Whenever the building commission determines that the use of innovative types of design and construction processes will make better use of the resources and technology available in the building industry, the building commission may waive any or all of s. 16.855, except s. 16.855 (13) and (14m) (a) to (c), if the action is in the best interest of the state and is approved by the building commission.
WS § 62.155 Acquisition of facilities without bids.
https://docs.legis.wisconsin.gov/statutes/statutes/62/i/155
A city may contract for the acquisition of any element of the following without submitting the contract for bids as required under s. 62.15 if the city invites developers to submit proposals to provide a completed project and evaluates proposals according to site, cost, design and the developers’ experience in other similar projects:
(1) A recycling or resource recovery facility.
(2) If the city contains an electronics and information technology manufacturing zone that is designated under s. 238.396 (1m):
(a) Water and sewer systems.
(b) Wastewater treatment facilities.
W. Va. Code § 5-22A-1 – 16
§5-22A-3. Public policy; conditions for contract.
https://code.wvlegislature.gov/5-22A-3/
(a) Recognizing that the design-bid-build method provides a viable delivery method for public projects, it is the public policy of this state to permit an agency to enter into design-build contracts for public projects.
(b) An agency may not enter into a design-build contract for a public project unless:
(1) The Department of Administration promulgates and publishes legislative rules pursuant to section six of this article, and consistent with this article for the solicitation and award of design-build contracts and adheres to this article and those rules;
(2) The agency, for each public project or projects procured pursuant to this article, determines that it is in the best interest of the public to enter into a design-build contract to complete the public project or projects and adheres to this article and the rules; and
(3) The Board established pursuant to section four of this article determines that the public project is appropriate as a design-build project utilizing the mandatory criteria as provided in section five of this article.
§5-22A-2. Definitions.
(1) “Agency” means all state departments, agencies, authorities, quasi-public corporations and all political subdivisions, including cities, counties, boards of education and public service districts and the individual representatives of the agency appointed to oversee or supervise the project.
RCWA 39.10.270
https://app.leg.wa.gov/RCW/default.aspx?cite=39.10.270
A public body may apply for certification to use the design-build or general contractor/construction manager contracting procedure, or both.
RCWA 39.10.300
https://apps.leg.wa.gov/RCW/default.aspx?cite=39.10.300
Subject to the requirements in RCW 39.10.250, 39.10.270, or 39.10.280, public bodies may utilize the design-build procedure, including progressive design-build, for public works projects in which the total project cost is over two million dollars and where:
(a) The construction activities are highly specialized and a design-build approach is critical in developing the construction methodology; or
(b) The projects selected provide opportunity for greater innovation or efficiencies between the designer and the builder; or
(c) Significant savings in project delivery time would be realized.
VA Code Ann. § 2.2-4303 (effective until January 1, 2025) Methods of Procurement.
https://law.lis.virginia.gov/vacode/title2.2/chapter43/section2.2-4303/
D. Construction may be procured only by competitive sealed bidding, except that competitive negotiation may be used in the following instances:
1. By any public body on a fixed-price design-build basis or construction management basis as provided in Chapter 43.1 (§ 2.2-4378 et seq.)
VA Code Ann. § 2.2-4382. Design-build or construction management contracts for local public bodies authorized.
https://law.lis.virginia.gov/vacode/title2.2/chapter43.1/section2.2-4382/
A. Any local public body may enter into a contract for construction on a fixed price or not-to-exceed price construction management or design-build basis, provided that the local public body (i) receives approval, if required, as provided in subsection B, (ii) complies with the requirements of this article, and (iii) has by ordinance or resolution implemented procedures consistent with the procedures adopted by the Secretary of Administration for utilizing construction management or design-build contracts.
P3:
VA Code Ann. § 56-575.2. Declaration of public purpose.
https://law.lis.virginia.gov/vacode/title56/chapter22.1/section56-575.2/
A. The General Assembly finds that:
3. There are inadequate resources to develop new education facilities, technology infrastructure and other public infrastructure and government facilities for the benefit of citizens of the Commonwealth, and there is demonstrated evidence that public-private partnerships can meet these needs by improving the schedule for delivery, lowering the cost, and providing other benefits to the public;
29 V.S.A. § 161
https://legislature.vermont.gov/statutes/section/29/005/00161
(2) When using the design-build construction delivery process, the Commissioner of Buildings and General Services shall publicly advertise or invite three or more bids. The award of a design-build contract shall be to the bidder determined by the Commissioner to be most responsive to evaluation criteria established by the Commissioner. Such criteria may include physical plant characteristics proposed, program response to space needs, ability of the design-build team, anticipated development schedule, and overall cost considerations, including alternates, allowances, and schedule of values.
State:
U.C.A. § 63G-6a-1302
https://le.utah.gov/xcode/Title63G/Chapter6A/63G-6a-S1302.html?v=C63G-6a-S1302_2022050420220504
(1) A rulemaking authority shall, by rule provide as many alternative methods of construction contracting management as determined to be feasible.
Local:
U.C.A. § 11-39-107
https://le.utah.gov/xcode/Title11/Chapter39/11-39-S107.html?v=C11-39-S107_2014040320140329
(2) A local entity may adopt procedures for the following construction contracting methods:
(a) construction manager/general contractor, as defined in Section 63G-6a-103;
(b) a method that requires that the local entity draft a plan, specifications, and an estimate for the building improvement or public works project; or
(c) design-build, as defined in Section 63G-6a-103, if the local entity consults with a professional engineer licensed under Title 58, Chapter 22, Professional Engineers and Professional Land Surveyors Licensing Act, or an architect licensed under Title 58, Chapter 3a, Architects Licensing Act, who has design-build experience and is employed by or under contract with the local entity.
P3:
U.C.A. § 63N-13-302
https://le.utah.gov/xcode/Title63N/Chapter13/63N-13-S302.html?v=C63N-13-S302_2023050320230503
(5) “Public-private partnership” means an arrangement or agreement between a government entity and one or more private persons to fund and provide for a public need through the development or operation of a public project in which the private person or persons share with the government entity the responsibility or risk of developing, owning, maintaining, financing, or operating the project.
DEL. CODE. 29.69.IV § 6962
https://delcode.delaware.gov/title29/c069/sc04/index.html
(13) Bid evaluation, contract award and execution procedure. —
a. The contracting agency shall award any public works contract within 30 days of the bid opening to the lowest responsive and responsible bidder, unless the agency elects to award on the basis of best value, in which case the election to award on the basis of best value shall be stated in the invitation to bid.
4. A. If the agency elects to award on the basis of best value, the agency must determine that the successful bidder is responsive and responsible, as defined in this subsection. The determination of best value shall be based upon objective criteria that have been communicated to the bidders in the invitation to bid. The following objective criteria shall be assigned a weight consistent with all of the following:
I. Price — must be at least 70% but no more than 90%.
II. Schedule — must be at least 10% but no more than 20%.
III. Performance — must be at least 10% but no more than 20%.
B. Performance criterion must be based on a contractor’s performance rating as determined by the agency’s performance-based rating system. The agency’s performance-based rating system must be based on previous contracting performance and may not be based on a set of prescriptive rules favoring a particular business model or business procedure. The performance-based rating system must be defined in regulations promulgated by the Secretary of the agency and must include a procedure for a contractor to appeal a performance-based rating.
C. A weighted average stated in the invitation to bid shall be applied to each criterion according to its importance to each project. The agency shall rank the bidder according to the established criteria and award to the highest ranked bidder.
b. A contract may be awarded to a bidder other than the lowest responsible and responsive bidder if, in the opinion of the contracting agency, the interest of the agency shall be better served by awarding the contract to another bidder. Such award shall be made only if the contracting agency makes a written determination of the award describing the reason or reasons why such award better serves the interest of the agency. The reason or reasons for making such award may include, but are not limited to, unsatisfactory performance on any previously awarded contract by the bidder being rejected.
TX Govt § Title 10. Subtitle F. Chapter 2269
https://statutes.capitol.texas.gov/Docs/GV/htm/GV.2269.htm
CMAR:
Subchapter F. Construction Manager at-Risk Method.
Sec. 2269.251. Contracts for facilities: construction manager-at-risk.
(c) A governmental entity may use the construction manager-at-risk method in selecting a general contractor for the construction, rehabilitation, alteration, or repair of a facility only as provided by this subchapter.
Design-Build:
Subchapter H. Design-Build Procedures for Certain Civil Works Projects
Sec. 2269.351.
(1) “Civil works project” means:
(A) roads, streets, bridges, utilities, water supply projects, water plants, wastewater plants, water distribution and wastewater conveyance facilities, desalination projects, wharves, docks, airport runways and taxiways, storm drainage and flood control projects, or transit projects;
Sec. 2269.353. Contracts for civil works projects: design-build. (a) A governmental entity may use the design-build method for the construction, rehabilitation, alteration, or repair of a civil works project. In using this method and in entering into a contract for the services of a design-build firm, the contracting governmental entity and the design-build firm shall follow the procedures provided by this subchapter.
P3:
TX Govt § Title 10. Subtitle F. Chapter 2267
https://statutes.capitol.texas.gov/Docs/GV/htm/GV.2267.htm
Sec. 2267.002. Declaration of public purpose; construction of chapter. (a) The legislature finds that:
(3) there are inadequate resources to develop new education facilities, technology and other public infrastructure, and government facilities for the benefit of the citizens of this state, and there is demonstrated evidence that partnerships between public entities and private entities or other persons can meet these needs by improving the schedule for delivery, lowering the cost, and providing other benefits to the public;
(4) financial incentives exist under state and federal tax provisions that encourage public entities to enter into partnerships with private entities or other persons to develop qualifying projects; and
(5) authorizing private entities or other persons to develop or operate one or more qualifying projects may serve the public safety, benefit, and welfare by making the projects available to the public in a more timely or less costly fashion.
Sec. 2267.065. Procurement guidelines.
(b) A responsible governmental entity may enter into a comprehensive agreement only in accordance with guidelines that require the contracting person to design and construct the qualifying project in accordance with procedures that do not materially conflict with those specified in:
(1) Subchapter G, Chapter 2269, for facilities projects described by Section 2269.302; or
(2) Subchapter H, Chapter 2269, for civil works projects as defined by Section 2269.351.
TN Code § 12-10-124 (2023)
https://law.justia.com/codes/tennessee/title-12/chapter-10/section-12-10-124/
(c)
(1) No authority shall contract for the construction of buildings or improvements, the expenditure for which is estimated, projected or budgeted to be in excess of ten thousand dollars ($10,000) but less than one million dollars ($1,000,000) except when such contract is made through a public advertisement and competitive bid process. Public advertisement shall be given at least ten (10) days in advance of accepting bids for such construction, and the authority shall award the contract to the lowest responsible and responsive bidder whose bid meets the requirements and criteria set forth in the invitation to bid.
(2)
(A) No authority shall contract for the construction of buildings or improvements, the expenditure for which is estimated, projected or budgeted to be one million dollars ($1,000,000) or more except when such contract is made either:
(i) Through a public advertisement and competitive bid process;
(ii) Through a request for proposals process which includes minimum required qualifications; or
(iii) Through a request for qualifications process which includes minimum required qualifications and a selection process pursuant to which multiple proposers are selected and prequalified to submit competitive bids.
B) Public advertisement shall be given at least ten (10) days in advance of accepting bids or proposals for such construction. If the authority uses the competitive bid process, the authority shall award the contract to the lowest responsible and responsive bidder whose bid meets the requirements and criteria set forth in the invitation to bid. If the authority uses the request for proposals process, the authority shall award the contract to the lowest responsible and responsive bidder who meets the minimum required qualifications. If the authority uses the request for qualifications process, the authority shall award the contract to the lowest pre-qualified bidder.
(4) Notwithstanding the foregoing provisions of this subsection (c), contractual arrangements for construction delivery methods other than the competitive bid method, such as, but not limited to, the construction manager method, the construction manager at risk method, and the design-build method, or for remodeling and maintenance, may be awarded by a request for proposals process as provided in subsection (d).
(d) The authority shall contract for all services, including construction management services and design-build services, through the process provided in subsection (c) or by a request-for-proposals process; provided, however, that no such process shall be required if the authority contracts with a provider of any such service for a project who has been selected by a municipal corporation who is a contracting party or lessee with respect to such project through…
SDCL § 15-18B-20 Design-build contracts.
https://sdlegislature.gov/Statutes/5-18B-20
A purchasing agency may enter into design-build contracts for public improvements, if the following conditions are met:
(1) The purchasing agency shall, prior to issuing any design-build request for proposals, establish and publish procedures for the solicitation and award of design-build contracts. The Bureau of Human Resources and Administration shall establish the procedures for the state. The procedures shall include the following:
(a) The procedure to select or designate a performance criteria developer utilizing a qualification based process and the procedure to prepare performance criteria;
(b) The procedures for the preparation and contents of a design-build request for proposals;
(c) The procedure and standards to be used to qualify or pre-qualify design-builders;
(d) The procedures for preparing and submitting proposals;
(e) The procedures for evaluating proposals;
(f) The procedures for negotiations between the purchasing agency and those submitting proposals prior to the acceptance of a proposal. The procedures shall contain safeguards to preserve confidential information and proprietary information supplied by those submitting proposals, consistent with § 5-18B-34;
(g) The procedures for awarding and executing design-build contracts;
(h) The procedures for awarding design-build contracts in the event of public emergencies as defined in § 5-18A-9; and
(i) The procedures for acting on formal protests relating to the solicitation or award of design-build contracts;
(2) The purchasing agency shall, for each public improvement under this section, make a determination that it is in the best interest of the public to enter into a design-build contract to complete the public improvement. The determination to utilize design-build and the basis for the determination shall be recorded in the project file or the minutes of the meeting of the governing board of the purchasing agency. In making this determination, design-build projects shall meet one or more of the following criteria:
(a) The purchasing agency requires a project design and construction time line that is faster than the traditional design/bid/build process would allow;
(b) The complexity of the project requires close coordination of design and construction expertise or an extreme amount of coordination;
(c) The purchasing agency requires early cost commitments; or
(d) The project can be defined at an early stage and the purchasing agency is able to specify all requirements; and
(3) The purchasing agency shall follow the procedures of other laws governing public improvement construction contracts to the extent such laws are compatible with the use of design-build contracts.
CMAR:
SDCL § 5-18B-44. Criteria for construction manager at-risk engagement.
https://sdlegislature.gov/Statutes/5-18B-44
Each qualification-based request for proposals required by subsection 5-18B-43(2)(b) to enter into a construction manager-at-risk services contract where the construction manager-at-risk intends to actually perform construction on the project, shall meet the following criteria:
(1) The purchasing agency shall, prior to issuing any request for proposals to enter in a construction management services contract, establish and publish procedures for the solicitation and award of such contracts, which procedures shall include the following: [see link]
(2) A request for proposals to enter into a construction management services contract shall contain the following elements:[see link]
(3) Notice of any request for proposals shall be advertised in accordance with the provisions of § 5-18A-14;
(4) After obtaining and evaluating proposals, a purchasing agency may accept the proposal it considers the most advantageous to the purchasing agency. Acceptance of a proposal shall be by written notice to the construction manager submitting the accepted proposal, and by simultaneously notifying in writing the other construction managers that their proposals were not accepted; and
(5) The purchasing agency shall reserve the right to reject any or all proposals submitted.
SC St § 11-35-3005
(1) The following project delivery methods are authorized for procurements relating to infrastructure facilities:
(a) design-bid-build;
(b) construction management at-risk;
(c) operations and maintenance
(d) design-build;
(e) design-build-operate-maintain; and
(f) design-build-finance-operate-maintain.
In addition, the board and state engineer may approve any combination of design, construction, finance, and services for operations and maintenance of an infrastructure facility.
Local:
SC St § 11-35-5320. Political subdivisions required to develop and adopt procurement laws.
All political subdivisions of the State shall adopt ordinances or procedures embodying sound principles of appropriately competitive procurement no later than July 1, 1983. The State Fiscal Accountability Authority, in cooperation with the Procurement Policy Committee and subdivisions concerned, shall create a task force to draft model ordinances, regulations, and manuals for consideration by the political subdivisions. The expenses of the task force shall be funded by the General Assembly. The task force shall complete its work no later than January 1, 1982. A political subdivision’s failure to adopt appropriate ordinances, procedures, or policies of procurement is not subject to the legal remedies provided in this code.
CMAR:
§ 37-2-27.1. Procurement of construction manager at-risk services — Written determination.
http://webserver.rilin.state.ri.us/Statutes/TITLE37/37-2/37-2-27.1.htm
(a) Prior to procuring construction manager at-risk services, the chief purchasing officer must sign a written determination documenting the following:
(1) That in accordance with the factors set forth in subsection (c) below, the general contractor method of construction management as provided under § 37-2-18 is not practicable for the construction of the project or will not result in the best value for the state;
(2) That the using agency has clearly identified in writing why the use of construction management at-risk method of construction management as defined under § 37-2-7(30) is appropriate for the building project;
(3) That the building project has an estimated construction value of five million dollars ($5,000,000) or more;
(4) That the using agency has in place written procedures to ensure fairness in competition, evaluation, and reporting of results at every stage in the procurement process;
(5) That the using agency has the capacity, a detailed plan, and procedures in place to effectively procure and manage construction management at-risk services for the project and has procured the services of a qualified owner’s program manager for the project, as set forth in § 37-2-7(32); and
(6) That the using agency has a detailed, written plan with clearly identified procedures to monitor and approve all reimbursable costs for the project.
Design-Build:
§ 37-2-31. Use of other types of contracts.
http://webserver.rilin.state.ri.us/Statutes/TITLE37/37-2/37-2-31.htm
Subject to the limitations of §§ 37-2-29 and 37-2-30, any type of contract which will promote the best interests of the state may be used.
Local:
§ 45-55-2. Method of source selection.
http://webserver.rilin.state.ri.us/Statutes/TITLE45/45-55/45-55-2.htm
Except as otherwise authorized by law, all municipal contracts shall be awarded by:
(1) Competitive sealed bidding, pursuant to § 45-55-5;
(2) Competitive negotiations, pursuant to § 45-55-6;
(3) Non-competitive negotiations, pursuant to §§ 45-55-7 and 45-55-8;
(4) Small purchase procedures, pursuant to § 45-55-9; and
(5) Qualification-based selection (QBS) process for architects/engineers pursuant to § 45-55-8.1, and program managers, construction managers, or construction managers at-risk pursuant to § 45-55-8.2.
62 PA.C.S. § 322(2)
https://www.legis.state.pa.us/cfdocs/legis/LI/consCheck.cfm?txtType=HTM&ttl=62&div=0&chpt=3&sctn=22&subsctn=0
(2) Promptly after the notice in such cases or promptly after any appropriation made to it becomes available, the department shall, if necessary, select an architect and/or an engineer in accordance with the selection procedures of section 905 (relating to procurement of design professional services) to design the work and prepare the specifications therefor. The department may, as an alternative, enter into a design/build contract in accordance with section 511 (relating to methods of source selection). Such design/build contracts shall be subject to the requirements of this act and the provisions of the act of August 15, 1961 (P.L.987, No.442), known as the Pennsylvania Prevailing Wage Act. Design/build contracts shall also be subject to the act of May 1, 1913 (P.L.155, No.104), entitled “An act regulating the letting of certain contracts for the erection, construction, and alteration of public buildings,” to the extent provided in paragraph (6).
https://www.oregon.gov/das/OPM/Pages/pi-alternative.aspx
The Public Improvement Alternative Contracting method enables an agency to use innovative techniques and processes to procure public improvement projects. Examples of contracts that use this method include:
An agency may use the Public Improvement Alternative Contracting method if it is procuring:
-An Energy Savings Performance Contract.
-An individual contract that has been exempted from the competitive bidding process.
-A class of contracts that has been exempted from the competitive bidding process.
The Public Improvement Alternative Contracting method may also be used for other applicable statutory exceptions (refer to ORS 279C.335(1)).
*Refer to the Public Works for more information on construction, reconstruction, major renovation or painting of a road, highway, building, structure or improvement project of any type that serves the public interest, or equals or exceeds $750,000 in agency funds, and other distinguishing criteria of a public works project.
OR. REV. STAT. §§ 279B.060
https://www.oregonlegislature.gov/bills_laws/ors/ors279B.html
Competitive sealed proposals. (1) A contracting agency may solicit and award a public contract for goods or services, or may award multiple public contracts for goods or services when specified in the request for proposals, by requesting and evaluating competitive sealed proposals.
Department of Justice
Chapter 137 — Division 49
Model Rules General Provisions Related to Public Contracts for Construction Services
https://secure.sos.state.or.us/oard/displayDivisionRules.action?selectedDivision=300
P3:
House Bill 4111 (2014)
https://legiscan.com/OR/text/HB4111/2014
Section 1:
(5) Public-private partnerships, in numerous forms, might be used to supplement traditional methods of financing and procuring public infrastructure projects.
61 O.S. § 202.1 (OSCN 2024)
https://accessible.oksenate.gov/sites/default/files/2019-12/os61.pdf
A. The design-build and construction management project delivery methods shall not be used without the written approval of the Director of the Office of Management and Enterprise Services, or the Director’s designee, when those projects are constructed for a state agency or by an act of the Legislature specifying design-build or at-risk construction management for a project. In all instances where the design-build project or at-risk construction management delivery method is authorized, construction administration shall be performed by the State Facilities Director, the SFD’s designee or designees, or otherwise by contract or contract provision approved by the Director of the Office of Management and Enterprise Services for construction administration by another party.
B. The use of design-build and construction management project delivery methods shall not interfere or inhibit the opportunity for subcontractors and trade contractors to openly and freely compete for subcontracts or trade contracts pursuant to the Public Competitive Bidding Act of 1974. The State Facilities Director, or designee, or the construction manager shall make the subcontracting and supply opportunities publicly known, as follows:
1. Whenever the estimated cost of the contract exceeds Fifty Thousand Dollars ($50,000.00), public notice shall be given by publication in a newspaper of general circulation and published in the county where the work, or the major part of the work, is to be done. Such notice by publication shall be published in two consecutive weekly issues of the newspaper, with the first publication thereof to be at least twenty-one (21) days prior to the date set for opening bids; and
2. Notice thereof shall be sent to one in-state trade or construction publication for the publication’s use and information whenever the estimated cost of the contract exceeds Fifty Thousand Dollars ($50,000.00); provided, however, this section shall not be construed to require the publication of such notice in such trade or construction publication or to require the provision of such notice to more than one in-state trade or construction publication or to any out-of-state trade or construction publication.
C. Bids shall be publicly opened at the time and place designated in the public notice. A representative of the State Facilities Director shall be present at the bid opening.
D. The provisions of subsection A of this section shall not apply to projects by contract pursuant to an interagency agreement under Section 581 of Title 74 of the Oklahoma Statutes or to projects a state agency performs solely with the staff of the agency.
E. The Office of Management and Enterprise Services shall, pursuant to the Administrative Procedures Act, promulgate rules to effect procedures, processes and design-build/construction management fee guidelines necessary to the fulfillment of its responsibilities under this section.
P3:
§74-5155. Selection of projects – Public-sector comparators.
http://webserver1.lsb.state.ok.us/OK_Statutes/CompleteTitles/os74.pdf
A. Selection of Projects. Any proposer or responsible state agency may submit to the Partnership Committee one or more proposals for partnership projects in connection with any public service. The Partnership Committee shall identify potential projects and public services for which a public-private partnership may be appropriate from those received from a proposer, a responsible state agency or those identified by the Partnership Committee itself. The Partnership Committee shall select such projects based on the partnership’s potential to improve public operational efficiencies, improve environmental performance, promote public safety, attract private investment in the state and minimize governmental liabilities.
OH ST § 153.693
https://codes.ohio.gov/ohio-revised-code/section-153.693
For every design-build contract, the public authority planning to contract for design-build services, in consultation with the criteria architect or engineer, shall evaluate the statements of qualifications submitted by design-build firms specifically regarding the project, including the design-build firm’s proposed architect or engineer of record. Following this evaluation, the public authority shall:
(1) Select and rank not fewer than three firms which it considers to be the most qualified to provide the required design-build services, except that the public authority shall select and rank fewer than three firms when the public authority determines in writing that fewer than three qualified firms are available;
(2) Provide each selected design-build firm with all of the following:
(a) A description of the project and project delivery;
(b) The design criteria produced by the criteria architect or engineer under section 153.692 of the Revised Code;
(c) A preliminary project schedule;
(d) A description of any preconstruction services;
(e) A description of the proposed design services;
(f) A description of a guaranteed maximum price, including the estimated level of design on which such guaranteed maximum price is based;
(g) The form of the design-build services contract;
(h) A request for a pricing proposal that shall be divided into a design services fee and a preconstruction and design-build services fee. The pricing proposal of each design-build firm shall include at least all of the following:
(i) A list of key personnel and consultants for the project;
(ii) Design concepts adhering to the design criteria produced by the criteria architect or engineer under section 153.692 of the Revised Code;
(iii) The design-build firm’s statement of general conditions and estimated contingency requirements;
(iv) A preliminary project schedule.
(3) Evaluate the pricing proposal submitted by each selected firm and, at its discretion, hold discussions with each firm to further investigate its pricing proposal, including the scope and nature of the firm’s proposed services and potential technical approaches;
(4) Rank the selected firms based on the public authority’s evaluation of the value of each firm’s pricing proposal, with such evaluation considering each firm’s proposed costs and qualifications;
(5) Enter into contract negotiations for design-build services with the design-build firm whose pricing proposal the public authority determines to be the best value under this section.
CMAR:
OH ST § 9.334
https://codes.ohio.gov/ohio-revised-code/section-9.334
A) Every public authority planning to contract for construction management services with a construction manager at risk shall evaluate the proposals submitted and select not fewer than three construction managers at risk the public authority considers to be the most qualified to provide the required construction management services, except that the public authority shall select and rank fewer than three when the public authority determines in writing that fewer than three qualified construction managers at risk are available.
OH ST § 9.335
https://codes.ohio.gov/ohio-revised-code/section-9.335
The requirements set forth in sections 9.33 to 9.334 of the Revised Code for the bidding, selection, and award of a construction management contract by a public authority prevail in the event of any conflict with a provision of Chapter 153. of the Revised Code.
CMAR:
48-01.2-18. Construction management – Governing body determinations.
https://ndlegis.gov/cencode/t48c01-2.pdf
1. Notwithstanding any other provision of law, a governing body may use the agency construction management or construction management at-risk delivery methods for construction of a public improvement if:
a. The agency construction manager has no common ownership or conflict of interest with the architect, landscape architect, or engineer involved in the planning and design of the public improvement or with any person engaged in the construction of the public improvement.
b. The construction manager at-risk has no common ownership or conflict of interest with the architect, landscape architect, or engineer involved in the planning and design of the public improvement.
2. Before utilizing the agency construction management or construction management at-risk delivery method, a governing body shall make the following determinations:
a. That it is in the best interest of the public to utilize the agency construction manager or construction manager at-risk public improvement delivery method.
b. That the agency construction manager or construction manager at-risk planning and design phase services will not duplicate services normally provided by an architect or engineer.
c. That the agency construction manager or construction manager at-risk construction services will be in addition to and not duplicate the services provided for in the architect and engineer contracts.
P3:
NDCC 48-02.1-03. Public authority may enter into development agreement.
https://ndlegis.gov/cencode/t48c02-1.pdf#nameddest=48-02p1-03
A public authority may solicit or accept proposals from private operators for the constructing, improving, rehabilitating, operating, managing, and owning of a fee-based facility that will be situated in an area subject to the public authority’s jurisdiction. After a hearing, the public authority may accept a proposal that it determines to be in the public interest. A public authority may negotiate and enter into a development agreement with any private
N.C.G.S.A. § 143‑128. Requirements for certain building contracts.
https://www.ncleg.gov/EnactedLegislation/Statutes/PDF/ByArticle/Chapter_143/Article_8.pdf
a1) Construction methods. – The State, a county, municipality, or other public body shall award contracts to erect, construct, alter, or repair buildings pursuant to any of the following methods:
(1) Separate‑prime bidding
(2) Single‑prime bidding
(3) Dual bidding pursuant to subsection (d1) of this section
(4) Construction management at risk contracts pursuant to G.S. 143‑128.1
(5) Alternative contracting methods authorized pursuant to G.S. 143‑135.26(9)
(6) Design‑build contracts pursuant to G.S. 143‑128.1A
(7) Design‑build bridging contracts pursuant to G.S. 143‑128.1B
(8) Public‑private partnership construction contracts pursuant to G.S. 143‑128.1C.
N.C.G.S.A. § 143-128.1A
https://www.ncleg.net/enactedlegislation/statutes/html/bysection/chapter_143/gs_143-128.1a.html
A governmental entity shall establish in writing the criteria used for determining the circumstances under which the design-build method is appropriate for a project, and such criteria shall, at a minimum, address all of the following:
(1) The extent to which the governmental entity can adequately and thoroughly define the project requirements prior to the issuance of the request for qualifications for a design-builder.
(2) The time constraints for the delivery of the project.
(3) The ability to ensure that a quality project can be delivered.
(4) The capability of the governmental entity to manage and oversee the project, including the availability of experienced staff or outside consultants who are experienced with the design-build method of project delivery.
(5) A good faith effort to comply with G.S. 143 128.2, G.S. 143 128.4, and to recruit and select small business entities. The governmental entity shall not limit or otherwise preclude any respondent from submitting a response so long as the respondent, itself or through its proposed team, is properly licensed and qualified to perform the work defined by the public notice issued under subsection (c) of this section.
(6) The criteria utilized by the governmental entity, including a comparison of the advantages and disadvantages of using the design-build delivery method for a given project in lieu of the delivery methods identified in subdivisions (1), (2), and (4) of G.S. 143 128(a1).
NM Stat § 13-1-119.1 (2023)
https://law.justia.com/codes/new-mexico/chapter-13/article-1/section-13-1-119-1/
A. Except for road and highway construction or reconstruction projects, a design and build project delivery system may be authorized when the state purchasing agent or a central purchasing office makes a determination in writing that it is appropriate and in the best interest of the state or local public body to use the system on a specific project. The determination shall be issued only after the state purchasing agent or a central purchasing office has taken into consideration the following criteria, which shall be used as the minimum basis in determining when to use the design and build process.
NJ Rev Stat § 52:35B-3 (State)
https://lis.njleg.state.nj.us/nxt/gateway.dll?f=templates&fn=default.htm&vid=Publish:10.1048/Enu
3. a. If a contracting unit determines in its discretion that the design-build approach meets their needs better than the traditional design-bid-build approach established under New Jersey public procurement statutes for the project or projects under consideration, it shall be the public policy of this State to permit that contracting unit to enter into design-build contracts as defined in section 2 of P.L.2021, c.71 (C.52:35B-2), provided the following conditions are met.
NJ Rev Stat § 40A:11-57 (Local)
https://lis.njleg.state.nj.us/nxt/gateway.dll?f=templates&fn=default.htm&vid=Publish:10.1048/Enu
27. a. If a contracting unit determines in its discretion that the design-build approach meets their needs better than the traditional design-bid-build approach established under New Jersey public procurement statutes for the project or projects under consideration, it shall be the public policy of this State to permit that contracting unit to enter into design-build contracts as defined in section 26 of P.L.2021, c.71 (C.40A:11-53), provided the following conditions are met [abbreviated]:
(1) The project or projects under consideration have a cost equal to or exceeding $5,000,000.
(3) The contracting unit shall, for each public project or projects under sections 26 through 33 of P.L.2021, c.71 (C.40A:11-53 through C.40A:11-60), make a determination based on the timeliness of the project or projects that it is in the best interest of the public to enter into a design-build contract to complete the public project or projects.
P3:
NJ Rev Stat § 40A:11-52 (Local)
https://lis.njleg.state.nj.us/nxt/gateway.dll?f=templates&fn=default.htm&vid=Publish:10.1048/Enu
b. (1) A local government unit may enter into a contract with a private entity, subject to subsection f. of this section, to be referred to as a public -private partnership agreement, that permits the private entity to assume full financial and administrative responsibility for a project of, or for the benefit of, the local government unit, provided that the project is financed in whole by the private entity and the local unit retains full ownership of the land upon which the project is located.
NY State Comptroller XI.18.H
https://www.osc.ny.gov/state-agencies/gfo/chapter-xi/xi18h-infrastructure-investment-act
The Infrastructure Investment Act allows for a design-build contract, an alternative delivery method, for capital projects located in New York State related to physical infrastructure undertaken by an “authorized state entity” subject to certain restrictions bulleted below.
• New York State Thruway Authority, the New York State Bridge Authority, the New York State Office of General Services, the Dormitory Authority of the State of New York, the New York State Urban Development Corporation, the State University Construction Fund, the New York State Olympic Regional Development Authority and the Battery Park City Authority for capital projects.
• New York State Department of Transportation; New York State Office of Parks, Recreation and Historic Preservation; New York State Department of Environmental Conservation; for capital projects with a total value of not less than $10 million.
• Other specified capital projects of specified contracting entities with a total value of not less than $5 million.
New York City:
NY SB 7636A
https://www.nysenate.gov/legislation/bills/2019/A7636/amendment/original
https://www.nyc.gov/assets/ddc/downloads/contracts/DB_Report_FINAL_2022.pdf
In December 2019, the governor signed the “New York City Public Works Investment Act” to permit several city agencies to use two-step design-build contracts. They include the Department of Design and Construction, Department of Environmental Protection, Department of Transportation, Department of Parks and Recreation, Health and Hospitals Corporation, School Construction Authority and Housing Authority.
Since publication of the 2021 Design-Build Progress Report, the City successfully advocated for and received a five-year extension of the PWIA from the State. In addition, the Department of Citywide Administrative Services (DCAS) was authorized to use design-build. The City recommends further modifying the PWIA to allow more flexibility in structuring design-build procurements to shrink procurement schedules, maximize collaboration between the City and proposing teams, and control costs. The City recommends that legislation permit a single-step RFP process (as opposed to a two-step process) referred to as progressive Design-build (PDB).
N.H. Rev. Stat § 21-I:80
https://www.gencourt.state.nh.us/rsa/html/I/21-I/21-I-80.htm
I. Each state project whose estimated cost is more than $25,000 shall be built under contracts awarded to the lowest qualified bidder who meets all project specifications through competitive bidding. The following are excluded from this competitive bidding requirement:
(d) Notwithstanding any other provision of law, the commissioner is authorized to use the design-build and construction management methods of contracting for any project. The capital project overview committee shall approve preliminary plans prior to construction, reconstruction, alteration, or maintenance if the project is part of a capital project and:
(1) The construction management method of contracting is used; or
(2) The design-build method of contracting is used and the estimated cost is more than $500,000. If the design-build method of contracting is used and the estimated cost is $500,000 or less, preapproval of the capital project overview committee shall not be required, but the department shall notify the committee of all such projects and shall provide quarterly reports on project status.
CMAR:
NRS § 338.1685 – 338.16995
https://www.leg.state.nv.us/NRS/NRS-338.html#NRS338Sec1685
338.169. 1. Subject to the provisions of subsection 2, a public body may construct a public work by:
(a) Selecting a construction manager at-risk pursuant to the provisions of NRS 338.1691 to 338.1696, inclusive; and
(b) Entering into separate contracts with a construction manager at-risk:
(1) For preconstruction services, including, without limitation:
(I) Assisting the public body in determining whether scheduling or constructability problems exist that would delay the construction of the public work;
(II) Estimating the cost of the labor and material for the public work; and
(III) Assisting the public body in determining whether the public work can be constructed within the public body’s budget; and
(2) To construct the public work.
2. A public body in a county whose population is less than 100,000 may enter into contracts with a construction manager at-risk pursuant to NRS 338.1685 to 338.16995, inclusive, for the construction of not more than two public works in a calendar year that are discrete projects.
Design-Build:
NRS § 338.1711 – 1727
https://www.leg.state.nv.us/NRS/NRS-338.html#NRS338Sec1711
338.1711. 2. A public body may contract with a design-build team for the design and construction of a public work that is a discrete project if the public body has approved the use of a design-build team for the design and construction of the public work and the public work has an estimated cost which exceeds $5,000,000.
*NRS § 338.1389
https://www.leg.state.nv.us/nrs/NRS-338.html#NRS338Sec1389
1. Except as otherwise provided in subsection 10 and NRS 338.1385, 338.1386 and 338.13864, a public body or its authorized representative shall award a contract for a public work for which the estimated cost exceeds $250,000 to the contractor who submits the best bid.
Design-Build (including PDB and CMAR):
Neb. Rev. St. § 13-2901 – 13-2914
https://nebraskalegislature.gov/laws/statutes.php?statute=13-2914
13-2904. 1) Notwithstanding the procedures for public lettings in sections 73-101 to 73-106 or any other statute relating to the letting of bids by a political subdivision, a political subdivision which follows the Political Subdivisions Construction Alternatives Act may solicit and execute a design-build contract or a construction management at-risk contract.
(3) of section 13-2914, the resolution shall include a statement that the political subdivision has made a determination that the design-build contract or construction management at risk contract delivery system is in the public interest based, at a minimum, on one of the following criteria: (a) Savings in cost or time or (b) requirement of specialized or complex construction methods suitable for the design-build contract or construction management at risk contract delivery system.
13-2914. (2) A city of the metropolitan class may use a design-build contract or construction management at-risk contract under the Political Subdivisions Construction Alternatives Act for the purpose of complying with state or federal requirements to control or minimize overflows from combined sewers.
(3) A political subdivision may use a design-build contract or construction management at-risk contract under the Political Subdivisions Construction Alternatives Act for a project, in whole or in part, for water, wastewater, utility, or sewer construction.
Neb. Rev. St. § 61-504
https://nebraskalegislature.gov/laws/statutes.php?statute=61-504
The department, in accordance with the Public Water and Natural Resources Project Contracting Act, may solicit and execute a design-build contract, a progressive design-build contract, or a construction manager-general contractor contract for a public surface water or groundwater-related infrastructure project.
P3:
Neb. Rev. St. § 61-520
https://nebraskalegislature.gov/laws/statutes.php?statute=61-520
(1) A public-private partnership delivery method may be used for projects under the Public Water and Natural Resources Project Contracting Act as provided in this section and rules and regulations adopted and promulgated pursuant to this section only to the extent allowed under the Constitution of Nebraska. State contracts using this method shall be awarded by competitive negotiation.
MCA 18-2-501 – 503
https://www.leg.mt.gov/bills/mca/title_0180/chapter_0020/part_0050/section_0020/0180-0020-0050-0020.html
18-2-502. (1) Subject to the provisions of this part, state agency or a governing body may use an alternative project delivery contract, provided that the proposal meets at least two of the following criteria:
a) The project has significant schedule ramifications and using the alternative project delivery contract is necessary to meet critical deadlines by shortening the duration of construction.
b) By using an alternative project delivery contract, the design process will contribute to significant cost savings.
c) The project presents significant technical complexities that necessitate the use of an alternative delivery project contract.
A state agency or a governing body may use an alternative project delivery contract, provided that the proposal meets at least two of the following criteria:
a) The project has significant schedule ramifications and using the alternative project delivery contract is necessary to meet critical deadlines by shortening the duration of construction.
b) By using an alternative project delivery contract, the design process will contribute to significant cost savings.
c) The project presents significant technical complexities that necessitate the use of an alternative delivery project contract.
CMAR:
V.A.M.S. 67.5050
https://www.revisor.mo.gov/main/OneSection.aspx?section=67.5050
2. Any political subdivision may use the construction manager-at-risk method for: civil works projects such as roads, streets, bridges, utilities, water supply projects, water plants, wastewater plants, water distribution and wastewater conveyance facilities, airport runways and taxiways, storm drainage and flood control projects, or transit projects commonly designed by professional engineers in excess of two million dollars; and noncivil works projects such as buildings, site improvements, and other structures, habitable or not, commonly designed by architects in excess of three million dollars. In using that method and in entering into a contract for the services of a construction manager-at-risk, the political subdivision shall follow the procedures prescribed by this section.
Design-Build:
V.A.M.S. 67.5060
https://www.revisor.mo.gov/main/OneSection.aspx?section=67.5060
16. (1) As used in this subsection, “wastewater or water contract” means any design-build contract that involves the provision of engineering and construction services either directly by a party to the contract or through subcontractors retained by a party to the contract for a wastewater or water storage, conveyance, or treatment facility project.
(2) Any political subdivision may enter into a wastewater or water contract for design-build of a wastewater or water project.
21. This section shall not apply to:
(1) Any metropolitan sewer district established under Article VI, Section 30(a) of the Constitution of Missouri; or
(2) Any special charter city, or any city or county governed by home rule under Article VI, Section 18 or 19 of the Constitution of Missouri that has adopted a design-build process via ordinance, rule, or regulation.
V.A.M.S. 249.425
https://www.revisor.mo.gov/main/OneSection.aspx?section=249.425&bid=13278&hl=design-build%u2044
2. (1) Notwithstanding any other provision of law to the contrary, any sewer district is authorized to enter into design-build contracts for design-build projects that exceed an expenditure of one million dollars.
V.A.M.S. 67.5070
https://www.revisor.mo.gov/main/OneSection.aspx?section=67.5070&bid=33855&hl=design-build%u2044
2. Any political subdivision may enter into a design-build contract for engineering, design, and construction of a wastewater or water treatment project.
3. In disbursing community development block grants under 42 U.S.C. Sections 5301 to 5321, the department of economic development shall not reject wastewater or water treatment projects solely for utilizing design-build.
4. The department of natural resources shall not preclude design-build contracts from consideration of funding provided by the water and wastewater loan fund established in section 644.122.
P3:
V.A.M.S. 227.600-227.669
https://www.revisor.mo.gov/main/OneSection.aspx?section=227.648&bid=12311&hl=
227.648. Agreements authorizing private partner regarding procurement. — The commission may by agreement authorize or require a private partner to exercise any of the following provisions regarding procurement for the financing, development, and/or operation of the project:
(1) Use any project delivery method for the efficient development and/or operation of the project. Such project delivery methods shall include but are not limited to project delivery methods established in section 8.285 or sections 227.100 and 227.107. In addition, the limitation in subsection 1 of section 227.107 on the number of design-build contracts authorized to be let by the commission shall not apply to the project;
(2) Make available to the commission, upon request, all procurement records for financing, development, and/or operation of the project;
(3) Exempt the project from the general procurement laws in chapter 34.
Design-Build:
Miss. Code Ann. § 31-7-13.1
Document Page Link
(1) The method of contracting for construction described in this section shall be known as the ” design-build method” of construction contracting. This method of construction contracting may be used on residential buildings, residential mixed-use developments, parking garages and other prescriptive type facilities. The design-build method of construction contracting may only be used when the Department of Finance and Administration or a governing authority has determined that it satisfies the public interest better than traditional design-bid or when the Legislature has specifically required or authorized the use of this method in the legislation authorizing a project. At a minimum, the determination must include a detailed explanation of why using the design-build method for a particular project satisfies the public need better than the traditional design-bid-build method based on the following criteria:
(a) The project provides a savings in time or cost over traditional methods; and
(b) The size and type of the project is suitable for design-build.
(2) For each proposed design-build project, either a fixed firm price or guaranteed maximum price contract must be adopted. Before solicitation of proposals, the agency or governing authority shall develop a scope of work statement that provides prospective offerors with sufficient information regarding the requirements of the agency or governing authority.
CMAR:
Miss. Code Ann. § 31-7-13.2
Document Page Link
(1) When used in this section, “construction manager at risk” means a method of project delivery in which a construction manager guarantees a maximum price for the construction of a project and in which the governing authority or board, before using this method of project delivery, shall include a detailed explanation of why using the construction manager at risk method of project delivery for a particular project satisfies the public need better than that traditional design-bid-build method based on the following criteria:
(a) The use of construction manager at risk for the project provides a savings in time or cost over traditional methods; and
(b) The size and type of the project is suitable for use of the construction management at risk method of project delivery.
(2) When the construction manager at risk method of project delivery is used:
(a) There may be a separate contract for design services and a separate contract for construction services;
(b) The contract for construction services may be entered into at the same time as a contract for the design services or later;
(c) Design and construction of the project may be in sequential or concurrent phases; and
(d) Finance, maintenance, operation, reconstruction or other related services may be included for a guaranteed maximum price.
(3) When procuring design professional services under a construction manager at risk project delivery method, the agency or governing authority shall procure the services of a design professional pursuant to qualifications-based selection procedures.
(4) Before the substantial completion of the design documents, the agency or governing authority may elect to hire a construction manager.
(5) When procuring construction management services, the agency or governing authority shall follow the qualifications-based selection procedures as outlined in subsection (10) of this section or the competitive sealed proposal procedures as outlined in Section 31-17-13.
(6) The agency or governing authority may require the architect or engineer and the construction manager, by contract, to cooperate in the design, planning and scheduling, and construction process. The contract shall not make the primary designer or construction manager a subcontractor or joint-venture partner to the other or limit the primary designer’s or construction manager’s independent obligations to the agency or governing authority.
(7) Notwithstanding anything to the contrary in this chapter:
(a) Each project for construction under a construction manager at risk contract shall be a specific, single project with a minimum construction cost of Twenty-five Million Dollars ($25,000,000.00).
(b) Each project under a construction manager at risk contract shall be a specific, single project. For the purposes of this paragraph, “specific, single project” means a project that is constructed at a single location, at a common location or for a common purpose.
State:
MSA §§ 16C.32
https://www.revisor.mn.gov/statutes/cite/16C.32
Subd. 2.Authority; design-build contract; construction manager at-risk.
(a) Subject to limitations in sections 16B.31, subdivision 1; 16B.33, subdivision 1; 16C.16; and 16C.32 to 16C.34, and notwithstanding any other law to the contrary, the commissioner may:
(1) solicit and award a design-build contract on the basis of either a qualifications based or a design and price-based selection process provided in section 16C.33 if the conditions in paragraph (b) are met;
(2) select a construction manager at risk as provided in section 16C.34, and award a guaranteed maximum price contract for a construction manager at risk if the conditions of paragraph (c) are met; and
Local:
MSA §§ 471.345 Uniform Municipal Contracting Law
https://www.revisor.mn.gov/statutes/cite/471.345
Subd. 3a.Contracts over $175,000; best-value alternative.
As an alternative to the procurement method described in subdivision 3, municipalities may award a contract for construction, alteration, repair, or maintenance work to the vendor or contractor offering the best value under a request for proposals as described in section 16C.28, subdivision 1, paragraph (a), clause (2), and paragraph (c).
Subd. 3b.Contracts over $175,000; construction manager at-risk alternative.
As an alternative to the procurement methods described in subdivisions 3 and 3a, municipalities may award a contract for construction, alteration, repair, or maintenance work to a construction manager at risk as provided in section 471.463.
Mass. Gen. Laws c.149A, §§ 14-21
https://malegislature.gov/laws/generallaws/parti/titlexxi/chapter149a/section14
Section 14. Notwithstanding section 39M of chapter 30, for each contract for the construction, reconstruction, alteration, remodeling or repair of a public works project by an awarding authority and estimated by the awarding authority to cost not less than $5,000,000, the awarding authority may utilize design-build for the construction, reconstruction, alteration, remodeling or repair of any public works project pursuant to this section and sections 15 to 21, inclusive; but, before using the design-build, the awarding authority shall seek the approval of the inspector general pursuant to section 16.
M.C.L.A. 18.1241
https://www.legislature.mi.gov/Laws/MCL?objectName=mcl-18-1241
(1) Except for the contracts permitted in section 240, a contract shall not be awarded for the construction, repair, remodeling, or demolition of a facility unless the contract is let pursuant to a bidding procedure that is approved by the board. The department shall issue directives prescribing procedures to be used to implement this section. The procedures shall require a competitive solicitation in the award of any contract for construction, repair, remodeling, or demolition of a facility.
(4) Subject to subsection (3), for projects funded in whole or part with state funds, the construction contract award shall be made to the responsive and responsible best-value bidder.
M.C.L.A. 18.1261
https://www.legislature.mi.gov/Laws/MCL?objectName=mcl-18-1261
(1) The department shall provide for the purchase of, the contracting for, and the providing of supplies, materials, services, insurance, utilities, third party financing, equipment, printing, and all other items as needed by state agencies for which the legislature has not otherwise expressly provided. If consistent with federal statutes, in all purchases made by the department, all other things being equal, preference shall be given to products manufactured or services offered by Michigan-based firms or by facilities with respect to which the operator is designated as a clean corporate citizen under part 14 of the natural resources and environmental protection act, 1994 PA 451, MCL 324.1401 to 324.1429, or to biobased products whose content is sourced in this state. The department shall solicit competitive bids from the private sector whenever practicable to efficiently and effectively meet the state’s needs. The department shall first determine that competitive solicitation of bids in the private sector is not appropriate before using any other procurement method for an acquisition.
(2) The department shall make all discretionary decisions concerning the solicitation, award, amendment, cancellation, and appeal of state contracts.
(3) The department shall utilize competitive solicitation for all purchases authorized under this act unless 1 or more of the following apply…
(14) The department shall develop policies and procedures that require all procurement contracts entered into by the department or a state agency, including departments that have delegated procurement authority under this act, to include performance-related liquidated damages or performance targets with incentives in all procurement contracts. The department shall also develop policies and procedures that require the department or state agency to enforce these provisions. Departments or state agencies acting under delegated authority shall inform the department of relevant performance issues. Exceptions to the inclusion or enforcement of performance-related contract provisions may only be granted by the department as provided in a written or electronic record by the department.
COMAR 21.05.11.02–21.05.11.04
https://dsd.maryland.gov/regulations/Pages/21.05.11.02.aspx
https://dsd.maryland.gov/regulations/Pages/21.05.11.04.aspx
.02 Determination on Use of the Design-Build Method.
Before the solicitation is issued, the procurement officer shall prepare a written determination justifying the use of the design-build method which addresses some or all of the following criteria:
A. The extent to which the unit can adequately define the project requirements;
B. Time constraints for delivery of the project;
C. Capability and experience of prospective contractors with the design-build method or similar experience;
D. Suitability of the project for use of the design-build method of project delivery with respect to time, schedule, costs, and quality factors; and
E. Capability of the agency to manage the project.
.04 Selection of the Design-Builder.
A. Selection of a design-builder shall be conducted using the multi-step sealed bid procurement method as provided in COMAR 21.05.02.17 or the competitive sealed proposals procurement method as provided in COMAR 21.05.03.
P3:
MD Code, State Finance and Procurement § 10A-103
https://casetext.com/statute/code-of-maryland/article-state-finance-and-procurement/division-i-state-finance/title-10a-public-private-partnerships/subtitle-1-definitions-general-provisions/section-10a-103-establishment-of-public-private-partnership-by-reporting-agency
(a)
(1) A reporting agency may establish a public-private partnership and execute an agreement in connection with any public infrastructure asset for which the reporting agency is responsible in accordance with the provisions of the Annotated Code.
MD Code, State Finance and Procurement § 3-602 – Capital Projects
https://casetext.com/statute/code-of-maryland/article-state-finance-and-procurement/division-i-state-finance/title-3-budget-and-management/subtitle-6-capital-program/section-3-602-capital-projects
(g) Total project funding may utilize alternative construction methods, such as: (1) design/build which involves a single solicitation to design and build the facility; or (2) “fast track” in which design and construction are implemented concurrently.
MD Code PUC § 20-104
https://casetext.com/statute/code-of-maryland/article-public-utilities/division-ii-washington-suburban-sanitary-commission/title-20-procurement/subtitle-1-water-and-sewer-procurement-contracts/section-20-104-design-and-construction-of-system-in-general?searchWithin=true&listingIndexId=code-of-maryland&q=design-build&type=statute&sort=relevance&p=1
(d)(1) Except as provided in paragraph (2) of this subsection, the Commission may enter into any type of contract under this subtitle that promotes the best interest of the Commission.(2) The Commission:(i) may not enter a cost-plus-percentage-of-cost contract; and(ii) shall prohibit a cost-plus-percentage-of-cost subcontract under a contract with the Commission.(e) The Commission may only enter into a design/build contract for a facilities construction contract with costs exceeding $2,000,000.
5 M.R.S.A. §1743
https://legislature.maine.gov/statutes/5/title5sec1743.html
3. Alternative methods of project delivery. As an alternative to the competitive bid method provided in subsection 2, a public improvement contract may be undertaken using the construction-manager-advisor, construction-manager-at-risk or design-build method of construction.
Local
La. Rev. Stat §33.2740.27 – Algiers Development District and La. Rev. Stat §33.2740.70 – Gentilly Development District
https://www.legis.la.gov/Legis/Law.aspx?d=89986
https://www.legis.la.gov/Legis/Law.aspx?d=631497
J.(1) Notwithstanding any law to the contrary, if the board determines, in its discretion, that it is in the best interest of the taxpayers and that completion of public improvements and facilities will be expedited, the design and construction phases of any project may be combined.
La. Rev. Stat §2740.70.1 – Downman Road Economic Development District
https://www.legis.la.gov/Legis/Law.aspx?d=815457
K.(1) Notwithstanding any other provision of law to the contrary, if the board determines, in its discretion, that it is in the best interest of the taxpayers and that completion of public improvements and facilities will be expedited, the design and construction phases of any project may be combined.
State
La. Rev. Stat §49:214.6.2
https://www.legis.la.gov/legis/law.aspx?d=672078
A. The authority shall administer the programs of the Coastal Protection and Restoration Authority Board. The executive director may use his contracting authority, or the contracting authority of any state department or agency, to implement the provisions of this Chapter. His contracting authority shall include construction management at-risk, operation and maintenance, design-build, design-build-operate and maintain, design-build-finance-operate and maintain, outcome-based performance contracts, or any combination of design, construction, finance, and services for operation and maintenance of an integrated coastal protection project, where appropriate.
CMAR
La. Rev. Stat §2225.2.4
https://www.legis.la.gov/legis/Law.aspx?d=919372
Notwithstanding any other provision of law to the contrary, a public entity may use the construction management at-risk project delivery method to contract for a project to construct public works as set forth in this Section. CMAR shall not be used for any project that is estimated to cost less than $5 million.
KRS §45A.075
https://apps.legislature.ky.gov/law/statutes/statute.aspx?id=44857
Except as otherwise authorized by law, all state contracts shall be awarded by:
(1) Competitive sealed bidding, pursuant to KRS 45A.080;
(2) Competitive negotiation, pursuant to KRS 45A.077, 45A.085, 45A.090, or 45A.180;
(3) Noncompetitive negotiation, pursuant to KRS 45A.095; or
(4) Small purchase procedures, pursuant to KRS 45A.100.
Effective:April 8, 2016
KRS §45A.045
https://apps.legislature.ky.gov/law/statutes/statute.aspx?id=22333
For capital construction projects, subject to the provisions of this code and KRS 45A.180, the procurement may be on whichever of the following alternative project
delivery methods, in the judgment of the secretary of the Finance and Administration Cabinet after first considering the traditional design-bid-build project delivery method, offers the best value to the taxpayer:
(a) A design-build basis; or
(b) A construction management-at-risk basis.
Proposals shall be reviewed by the engineering staff to assure quality and value, and compliance with procurement procedures. All specifications shall be written to promote competition. Nothing in this section shall prohibit the procurement ofphased bidding or construction manager-agency services.
Effective: June 20, 2005
KRS §45A.180
https://apps.legislature.ky.gov/law/statutes/statute.aspx?id=44585
The secretary of the Finance and Administration Cabinet shall promulgate administrative regulations by October 15, 2003, providing for as many alternative methods of management of construction contracting as he or she may determine to be feasible; setting forth criteria to be used in determining which method of management of construction is to be used for a particular project; establishing a model process parallel to the selection committee procedures established in 45A.810 for the procurement of alternative project services of “construction management-at-risk” and “design-build,” and for a “construction manager-general contractor” and a “construction manager-agency;” and providing that the chief purchasing officer shall execute and include in the contract file a written statement setting forth the facts recommending that a particular method of management of construction contracting be used.
Effective June 24, 2015
KRS §65.025 (local)
https://apps.legislature.ky.gov/law/statutes/statute.aspx?id=44859
All local governments are authorized to use design-build using best-value procurement and contracting principles and P3 as long as the provisions of KRS 65.028 are followed.
A local government shall not employ the same entity to provide both architectural services and construction management services on the same capital construction project.
Effective April 8, 2016
P3:
KRS §45A.077
https://apps.legislature.ky.gov/law/statutes/statute.aspx?id=53096
A public-private partnership delivery method may be utilized as provided in this section and administrative regulations promulgated thereunder. State contracts
using this method shall be awarded by competitive negotiation.
Effective: July 14, 2022
DB and CMAR (state)
K.S.A. 75-37, 143 (2023)
https://www.kslegislature.org/li/b2023_24/statute/075_000_0000_chapter/075_037_0000_article/075_037_0143_section/075_037_0143_k/
Same; state building advisory commission authorized to institute alternative project delivery program; acquisition of information from potential contractors; determination of project appropriateness; notices and public hearing regarding program request; rules and regulations. (a) Notwithstanding any other provision of the law to the contrary, the state building advisory commission is hereby authorized to institute an alternative project delivery program whereby construction management at-risk or building design-build procurement processes may be utilized on state agency public projects pursuant to this act. This authorization for construction management at-risk and building design-build procurement shall be for the sole and exclusive use of planning, acquiring, designing, building, equipping, altering, repairing, improving, or demolishing any structure or appurtenance thereto, including facilities, utilities, or other improvements to any real property, but shall not include highways, roads, bridges, dams, turnpikes or related structures, or stand-alone parking lots.
Design-Build (local)
K.S.A. 19-216d (2023)
https://www.kslegislature.org/li/b2023_24/statute/019_000_0000_chapter/019_002_0000_article/019_002_0016d_section/019_002_0016d_k/
Criteria for use. (a) Notwithstanding any other provision of the law to the contrary, the board is hereby authorized to institute an alternative project delivery program whereby construction management at-risk or building design-build procurement processes may be utilized on public projects pursuant to this act. This authorization for construction management at-risk and building design-build procurement shall be for the sole and exclusive use of planning, acquiring, designing, building, equipping, altering, repairing, improving or demolishing any structure or appurtenance thereto, including facilities, utilities or other improvements to any real property, but shall not include highways, roads, bridges, dams or related structures or stand-alone parking lots.
(b) The board may only approve those projects or programs for which the use of alternative project delivery procurement process is appropriate.
CMAR (local)
K.S.A. 19-216e (2023)
https://www.kslegislature.org/li/b2023_24/statute/019_000_0000_chapter/019_002_0000_article/019_002_0016e_section/019_002_0016e_k/
Procedure, construction management at-risk. Construction management at-risk project delivery procedures shall be conducted as follows:
(a) The board shall determine the scope and level of detail required to permit qualified firms to submit construction management at-risk proposals in accordance with the request for proposals given the nature of the project.
HRS § 103D-303
https://www.capitol.hawaii.gov/hrscurrent/Vol02_Ch0046-0115/HRS0103D/HRS_0103D-0303.htm
(a) Competitive sealed proposals may be used to procure goods, services, or construction that are either not practicable or not advantageous to the State to procure by competitive sealed bidding.
(g) Award shall be made to the responsible offeror whose proposal is determined in writing to be the most advantageous, taking into consideration price and the evaluation factors set forth in the request for proposals. No other factors or criteria shall be used in the evaluation. The contract file shall contain the basis on which the award is made.
(i) In addition to any other provisions of this section, construction projects may be solicited through a request for proposals to use the design-build method; provided that:
(1) A request for proposals is issued to prequalify offerors to select a short list of no more than three responsible offerors, prior to the submittal of proposals; provided that the number of offerors to be selected for the short list shall be stated in the request for proposals and prompt notice is given to all offerors as to which offerors have been short-listed;
(2) A conceptual design fee may be paid to non-selected offerors that submit a technically responsive proposal; provided that the cost of the entire project is greater than $1,000,000;
(3) The criteria for pre-qualification of offerors, design requirements, development documents, proposal evaluation criteria, terms of the payment of a conceptual design fee, or any other pertinent information shall be stated in the request for proposals; and
(4) Past performance on projects of similar scope for public agencies or private industries shall be an evaluation factor for the prequalification of offerors.
I.C. § 67-5711A
https://legislature.idaho.gov/statutesrules/idstat/title67/t67ch57/sect67-5711a/
Notwithstanding any other provisions of law to the contrary, the director of the department of administration, or his designee, is authorized and empowered, subject to the approval of the permanent building fund advisory council, to employ the use of the design-build method of construction in the letting of any and all contracts for the construction, alteration, equipping, furnishing and repair of any and all buildings, improvements, or other public works of the state of Idaho.
(1) A design-build contract is a contract between the state of Idaho and a nongovernmental party in which the nongovernmental party contracting with the state of Idaho agrees to both design and build the structure, roadway, or other items specified in the contract;
I.C. § 67-2309
https://legislature.idaho.gov/statutesrules/idstat/title67/t67ch23/sect67-2309/
The design-build method of construction may be employed by public officials in contracts for the construction, repair, or improvement of public works, public buildings, public places or other work. For purposes of this section, a design-build contract is a contract between a public entity and a nongovernmental party in which the nongovernmental party contracting with the public entity agrees to both design and build a structure, roadway or other item specified in the contract.
Effective 6-14-2022: Senate File 183, an Act relating to a construction manager-at-risk commercial construction alternative delivery method and prohibiting certain other alternative delivery methods in the public sector and including effective date and applicability provisions:
Sec. 2. Section 262.34, Code 2021, is amended by adding the following new subsection: NEW SUBSECTION. 6.
The state board of regents shall not be authorized to enter into a design-build contract to construct, repair, or improve buildings or grounds.
CMAR (allowed):
Sec. 6. NEW SECTION. 26A.2 Authorization.
Notwithstanding any other law to the contrary, a governmental entity shall be authorized to enter into a guaranteed maximum price contract for the construction of a
public improvement pursuant to this chapter.
I.C.A. 26.9 –
https://www.legis.iowa.gov/docs/code/26.9.pdf
The contract for the public improvement must be awarded to the lowest responsive, responsible bidder. However, contracts relating to public utilities or extensions or improvements thereof, as described in sections 384.80 through 384.94, may be awarded by the City as it deems to be in the best interests of the City.
AK Stat. § 36.30.200 (2023)
https://www.akleg.gov/basis/statutes.asp#36.30.200
Except as otherwise provided in this chapter, or unless specifically exempted by law, an agency contract shall be awarded by competitive sealed proposals if it is not awarded by competitive sealed bidding.
When the commissioner of transportation and public facilities determines that it is advantageous to the state, a procurement officer may issue a request for proposals requesting the submission of offers to provide
(1) construction in accordance with a design provided by the offeror; request for proposals issued under this paragraph must require that each proposal submitted contain a single price that includes the design-build; or
(2) preconstruction and construction services under a single construction manager general contractor contract awarded under AS 36.30.309.
2 AAC 12.931 – 12.949
https://casetext.com/regulation/alaska-administrative-code/title-2-administration/chapter-12-procurement/article-16-design-build-construction-contracts/section-2-aac-12933-general-design-build-requirements
The procurement officer may conduct a design-build procurement process only if the commissioner of transportation and public facilities determines in writing that it is advantageous to the state.
https://casetext.com/regulation/alaska-administrative-code/title-2-administration/chapter-12-procurement/article-16-design-build-construction-contracts/section-2-aac-12933-general-design-build-requirements
CMAR/CMGC:
Ak. Stat. § 36.30.309
https://www.akleg.gov/basis/statutes.asp#36.30.309
The Department of Transportation and Public Facilities may award by competitive sealed proposals a construction manager general contractor contract in which the department awards a two-phase contract for a construction manager to be responsible for providing preconstruction services during the design phase of the project and, if an agreed-on price for constructing the project is reached, general contractor services during the construction phase.
Alaska is not currently enabled for P3.
https://aiai-infra.info/wp-content/uploads/P3-Snapshot-ALASKA.pdf
IC 5-30-1-1 through IC 5-30-8-5
https://iga.in.gov/laws/2023/ic/titles/5#5-30
A design-build contract awarded as provided in this article is valid and enforceable.
Before entering into a design-build contract, a public agency must appoint a technical review committee of at least three (3) individuals: A representative of the public agency; At least two of the following, but not more than one under each clause:
(A) An architect registered under IC 25-4
(B) A professional engineer registered under IC 25-31
(C) A qualified contractor under IC 4-13.6 or an individual employed by the qualified contractor
CMc (state)
https://iga.in.gov/laws/2023/ic/titles/5#5-32
IC 5-32-3-7 CMc performance of work
Sec. 7. A CMc may perform a part of the work only if:
(1) the public agency approves of the CMc’s performance of the work;
(2) the CMc would be awarded a contract for the work under the applicable contract award standard; and
(3) the CMc performs only such work that equals not more than twenty percent (20%) of the total value of the project.
CMAR (local)
https://iga.in.gov/laws/2023/ic/titles/5#5-16-10
IC 5-16-10-2 Limitations on employment of construction managers; contracts with construction managers prohibited.
Sec. 2. (a) A unit of local government may not employ the architect or engineer who provided design services on a public construction project or his affiliate, to be the construction manager on the project he designed.
(b) A unit of local government may not let a general contract, or any separate trade contract, to perform work on a public construction project to the construction manager of the project.
P3
IC 5-23 Public-Private Agreements
https://iga.in.gov/laws/2023/ic/titles/5#5-23
IC 5-23-1-3
Sec. 3. (a) The state or a political subdivision may enter into a public-private agreement with an operator under the terms of this article.
IC 5-23-3-1 Agreements between governmental body and operator
Sec. 1. A governmental body may enter into a BOT agreement with an operator for the acquisition, planning, design, development, reconstruction, repair, maintenance, or financing of any public facility on behalf of the governmental body.
30 ILCS 537/5 (state) [Section scheduled to be repealed on January 1, 2026]
https://witnessslips.ilga.gov/legislation/ilcs/ilcs3.asp?ActID=2758&ChapterID=7
It is the intent of the General Assembly that the State construction agency be allowed to use the design-build delivery method for public projects if it is shown to be in the State’s best interest for that particular project.
30 ILCS 537/30 [Section scheduled to be repealed on January 1, 2026]
(a) The State construction agency must use a two-phase procedure for the selection of the successful design-build entity. Phase I of the procedure will evaluate and shortlist the design-build entities based on qualifications, and Phase II will evaluate the technical and cost proposals.
30 ILCS 537/35 [Section scheduled to be repealed on January 1, 2026]
Small projects. In any case where the total overall cost of the project is estimated to be less than $10 million, the State construction agency may combine the two-phase procedure for selection described in Section 30 into one combined step, provided that all the requirements of evaluation are performed in accordance with Section 30.
65 ILCS 5/11-39.2-5 (local)
https://witnessslips.ilga.gov/legislation/ilcs/ilcs4.asp?DocName=006500050HArt%2E+11+Div%2E+39%2E2&ActID=802&ChapterID=14&SeqStart=181200000&SeqEnd=182500000
The purpose of this Division is to authorize municipalities to use design-build processes to increase the efficiency and effectiveness of delivering public projects.
65 ILCS 5/11-39.2-25
Procedures for Selection.
(a) The municipality must use a two-phase procedure for the selection of the successful design-build entity. Phase I of the procedure will evaluate and shortlist the design-build entities based on qualifications, and Phase II will evaluate the technical and cost proposals.
65 ILCS 5/11-39.2-30
Small projects. In any case where the total overall cost of the project is estimated to be less than $12,000,000, the municipality may combine the two-phase procedure for selection described in Section 11-39.2-25 into one combined step if all the requirements of evaluation are performed in accordance with Section 11-39.2-25.
65 ILCS 5/11-39.2-50
Exception. Nothing in this Division prevents a municipality from using a qualification-based selection process for design professionals or construction managers for design-build projects.
FL § 287.055 (9) (c)
http://www.leg.state.fl.us/Statutes/index.cfm?App_mode=Display_Statute&URL=0200-0299/0287/Sections/0287.055.html
Except as otherwise provided in s. 337.11(7), the Department of Management Services shall adopt rules for the award of design-build contracts to be followed by state agencies. Each other agency must adopt rules or ordinances for the award of design-build contracts. Municipalities, political subdivisions, school districts, and school boards shall award design-build contracts by the use of a competitive proposal selection process as described in this subsection, or by the use of a qualifications-based selection process pursuant to subsections (3), (4), and (5) for entering into a contract whereby the selected firm will, subsequent to competitive negotiations, establish a guaranteed maximum price and guaranteed completion date. If the procuring agency elects the option of qualifications-based selection, during the selection of the design-build firm the procuring agency shall employ or retain a licensed design professional appropriate to the project to serve as the agency’s representative.
FL §255.20 (local)
https://www.flsenate.gov/Laws/Statutes/2023/255.20
A county, municipality, special district as defined in chapter 189, or other political subdivision of the state seeking to construct or improve a public building, structure, or other public construction works must competitively award to an appropriately licensed contractor each project that is estimated to cost more than $300,000. For electrical work, the local government must competitively award to an appropriately licensed contractor each project that is estimated to cost more than $75,000. As used in this section, the term “competitively award” means to award contracts based on the submission of sealed bids, proposals submitted in response to a request for proposal, proposals submitted in response to a request for qualifications, or proposals submitted for competitive negotiation. This subsection expressly allows contracts for construction management services, design-build contracts, continuation contracts based on unit prices, and any other contract arrangement with a private sector contractor permitted by any applicable municipal or county ordinance, by district resolution, or by state law.
P3 (County, municipality, or special district):
FL §255.065
http://www.leg.state.fl.us/Statutes/index.cfm?App_mode=Display_Statute&Search_String=&URL=0200-0299/0255/Sections/0255.065.html”
(3) PROCUREMENT PROCEDURES – A responsible public entity may receive unsolicited proposals or may solicit proposals for a qualifying project and may thereafter enter into a comprehensive agreement with a private entity, or a consortium of private entities, for the building, upgrading, operating, ownership, or financing of facilities.
FL §153.90 (state)
https://www.flsenate.gov/Laws/Statutes/2020/0153.90
(2) The Legislature therefore determines that it is in the public interest of the state to supplement and enhance the authority of public entities to solicit, negotiate, and enter into contracts with private entities for the financing, designing, acquisition, ownership, leasing, construction, improvement, operation, maintenance, and administration, or any combination thereof, of wastewater facilities.
The Clean Water Fund (SRF) program in CT does not allow the use of design-build project delivery methods. CT-CWF program requires all projects to go through the design-bid-build process. CWF is the primary financial program in CT for municipal water and wastewater projects. Local governments will have their own requirements for procuring engineering or construction services which they can employ if local funds are being used. However, municipal governments pursuing CWF funds will need to abide by the programmatic and regulatory requirements under the CWF program in order to remain eligible for CWF funding assistance. CWF’s procurement requirements will supersede local requirements.
C.G.S.A. § 58, Sec. 4a-59
https://www.cga.ct.gov/current/pub/chap_058.htm#sec_4a-59
(c) All open market orders or contracts shall be awarded to (1) the lowest responsible qualified bidder, the qualities of the articles to be supplied, their conformity with the specifications, their suitability to the requirements of the state government and the delivery terms being taken into consideration and, at the discretion of the Commissioner of Administrative Services, life-cycle costs and trade-in or resale value of the articles may be considered where it appears to be in the best interest of the state, (2) the highest scoring bidder in a multiple criteria bid, in accordance with the criteria set forth in the bid solicitation for the contract, or (3) the proposer whose proposal is deemed by the awarding authority to be the most advantageous to the state, in accordance with the criteria set forth in the request for proposals, including price and evaluation factors. Notwithstanding any provision of the general statutes to the contrary, each state agency awarding a contract through competitive negotiation shall include price as an explicit factor in the criteria in the request for proposals and for the contract award.
CRS § 24-92-108 (2024) State Government
https://colorado.public.law/statutes/crs_24-92-108
Subject to the limitations of this section, any type of contract which will promote the best interests of the agency of government may be used; except that the use of a cost-plus-a-percentage-of-cost contract is prohibited. A cost-reimbursement contract may be used only when a determination is made in writing that such contract is likely to be less costly to the agency of government than any other type of contract or that it is impracticable to obtain the construction required unless the cost-reimbursement contract is used.
CRS § 24-93-104
https://colorado.public.law/statutes/crs_24-93-104
Notwithstanding any other provision of law, any agency may award an IPD contract for a public project in accordance with the provisions of this article upon the determination by such agency that integrated project delivery represents a timely or cost-effective alternative for a public project.
CRS § 30-20-1104 – 30-20-1108 County Government
https://colorado.public.law/statutes/crs_30-20-1104
Notwithstanding any other provision of law, any agency may award an IPD contract for a public project under the provisions of this part 11 upon the determination by such agency that integrated project delivery represents a timely or cost-effective alternative for a public project.
CRS § 31-25-1304 City/Town Government
https://colorado.public.law/statutes/crs_31-25-1304
Same as county.
CRS § 32-1-1804
https://colorado.public.law/statutes/crs_32-1-1804
Same as county/city/town.
PCC § 22160 – 22169 Local Agency DB Projects and PCC § 10187 State Agency DB Projects (same as below but repealed as of Jan 1, 2025)
The Legislature finds and declares that the design-build method of project delivery, using a best-value procurement methodology, has been authorized for various agencies that have reported benefits from such projects including reduced project costs, expedited project completion, and design features that are not achievable through the traditional design-bid-build method. (until Jan. 31, 2031)
Progressive Design-Build:
https://leginfo.legislature.ca.gov/faces/billTextClient.xhtml?bill_id=202320240SB706&search_keywords=progressive+design-build
CA SB 706 (October 8, 2023)
Existing law authorizes the Director of General Services to use the progressive design-build procurement process for the construction of up to 3 capital outlay projects, as jointly determined by the Department of General Services and the Department of Finance, and prescribes that process. Existing law defines “progressive design-build” as a project delivery process in which both the design and construction of a project are procured from a single entity that is selected through a qualifications-based selection at the earliest feasible stage of the project. Existing law, until January 1, 2029, authorizes local agencies, defined as any city, county, city and county, or special district authorized by law to provide for the production, storage, supply, treatment, or distribution of any water from any source, to use the progressive design-build process for up to 15 public works projects in excess of $5,000,000 for each project, similar to the progressive design-build process authorized for use by the Director of General Services. Existing law requires a local agency that uses the progressive design-build process to submit, no later than January 1, 2028, to the appropriate policy and fiscal committees of the Legislature a report on the use of the progressive design-build process containing specified information, including a description of the projects awarded using the progressive design-build process. Existing law requires the design-build entity and its general partners or joint venture members to verify specified information under penalty of perjury. This bill would, until January 1, 2030, provide additional authority for cities, counties, cities and counties, or special districts to use the progressive design-build process for up to 10 public works in excess of $5,000,000, not limited to water-related projects, excluding projects on state-owned or state-operated facilities. The bill would require information to be provided under penalty of perjury and would require similar reports due no later than December 31, 2028.
CMAR:
https://leginfo.legislature.ca.gov/faces/codes_displaySection.xhtml?sectionNum=20146.&lawCode=PCC
PCC § 20146
(a) A county, with approval of the board of supervisors, or a public entity, with approval of its governing body, may utilize construction manager at-risk construction contracts for the erection, construction, alteration, repair, or improvement of any infrastructure, excluding roads, and including, but not limited to, buildings, utility improvements associated with buildings, flood control and underground utility improvements, and bridges, owned or leased by the county. A construction manager at-risk construction contract may be used only for projects in the county in excess of one $1,000,000 and may be awarded using either the lowest responsible bidder or best-value method to a construction manager at-risk entity that possesses or that obtains sufficient bonding to cover the contract amount for construction services and risk and liability insurance as may be required by the county or public entity. Any payment or performance bond written for the purposes of this section shall be written using a bond form developed by the county or public entity.
PCC § 5956.4
A governmental agency may solicit proposals and enter into agreements with private entities for the design, construction, or reconstruction by, and may lease to, private entities for the following types of fee-producing infrastructure projects:…
(b) Drainage
(d) Water supply, treatment, distribution
(e) Flood control
(h) Municipal improvements
(m) Purification of water
(n) Sewage treatment, disposal, and water recycling
(p) Structures or buildings, except for sporting or entertainment events
ASA. § 22-9-203(j)(1))
Document Page Link
Notwithstanding any other provision of law to the contrary, a municipality, sanitation authority, water system, or consolidated waterworks system may enter into contracts with private persons, firms, associations, corporations, joint ventures, or other legal entities, including a combination of any of those entities, to provide for the design, building, operation, or maintenance, including a combination of those activities, of all or any portion of its wastewater system, stormwater system, water system, solar energy generation equipment and facilities, other capital asset, or any combination of those systems and assets.
A.C.A. § 14-235-226 (b) (1) and (2)
Document Page Link
(1) In addition to other applicable law on a municipal sewage system’s procurement authority, a municipal sewage system created and operating under this subchapter that employs or contracts with a licensed professional engineer to assist in project-scope development and to oversee construction observation for the benefit of the owner may use design-build construction for projects that exceed two million dollars ($2,000,000).
(2) In addition to other applicable law on a municipal sewage system’s procurement authority, a municipal sewage system created and operating under this subchapter may use general contractor construction management as a project delivery method for projects of any amount for building, altering, repairing, improving, maintaining, or demolishing any structure associated with the municipal sewage system.
A.C.A. § 22-10-102
Document Page Link
It is necessary to authorize the formation of public-private partnerships that may result in the ability to develop private projects for public infrastructure and governmental facilities in a more cost-efficient and timely manner, resulting in increased benefits to the public safety and welfare of the citizens of the state and substantial cost benefits to the governmental entities and the public.
Ariz. Rev. Stat. §§ 34-602-605 and Ariz. Rev. Stat §§ 41-2582
https://www.azleg.gov/viewdocument/?docName=https://www.azleg.gov/ars/34/00602.htm
https://www.azleg.gov/viewdocument/?docName=https://www.azleg.gov/ars/41/02582.htm
An agent/purchasing agent may procure design services, construction and construction services, as applicable, under any of the following project delivery methods:
design-bid-build, construction manager at-risk, design-build, job-order contracting.
Other pertinent legislation:
Ariz. Rev. Stat. § 41-2578
https://www.azleg.gov/viewdocument/?docName=https://www.azleg.gov/ars/41/02578.htm
Al. Code § 39-2-2
Design-build and CMAR are not currently allowed for water projects.
P3 allowances are unclear.
O.C.G.A. § 50-5-67(a), (b) (State)
Document Page Link
(a) Except as otherwise provided in this Code section, contracts exceeding $100,000.00 shall be awarded by competitive sealed bidding.
b)(1) Except as otherwise provided for in this part, all contracts for the purchase of supplies, materials, equipment, or services made under this part… shall, wherever possible, be based upon competitive bids and shall be awarded to the lowest responsible bidder…
Ga. Code Ann. §36-91-20 (c) (Local)
Document Page Link
(c) Governmental entities are authorized to utilize any construction delivery method, provided that all public works construction contracts subject to the requirements of this chapter that:
(1) Place the bidder or offeror at risk for construction; and
(2) Require labor or building materials in the execution of the contract
shall be awarded on the basis of competitive sealed bidding or competitive sealed proposals. Governmental entities shall have the authority to reject all bids or proposals or any bid or proposal that is nonresponsive or not responsible and to waive technicalities and informalities.
P3
Ga. Code Ann. §36-60-15.1 (Local)
Document Page Link
Notwithstanding any other provision of law to the contrary, any county or municipal corporation of this state is authorized, in the discretion of its governing authority, to enter into valid and binding leases and contracts with private persons, firms, associations, or corporations for any period of time not to exceed 20 years to provide for the operation and maintenance of all or a portion of its waste-water treatment system, storm-water system, water system, or sewer system, or any combination of such systems, which leases and contracts may include provisions for the design, construction, repair, reconditioning, replacement, maintenance, and operation of the system, or any combination of such services and functions.